CNCサイクロン集塵システム [サイクロン集塵器]
飛び散る粉じんを集塵機のノズルを構えて吸い取る様子(^^ゞ)
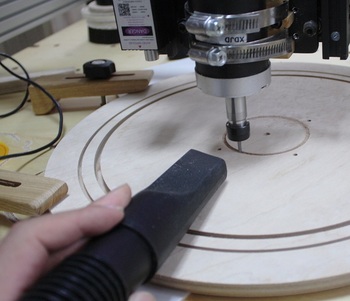
これはさすがみめんどくさいので、1年以上前だがCNC用の新しいサイクロンシステムを作る。
サイクロン部は中華製の既製品。


まず問題となるのは、サイクロン部と集塵容器部の接続・固定
集塵容器は、今までのサイクロンと同じ16L塗料容器を使う。
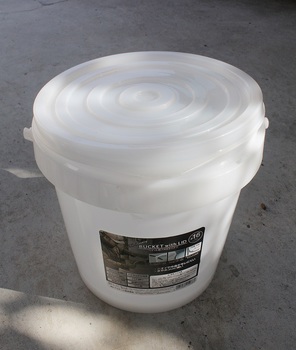
半透明で、ダストの溜まり具合が一目でわかるのがいい。
これにかぶせる木製蓋をCNCで切り出しサイクロン部を接合する
蓋の作図
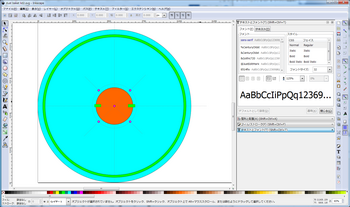
中心にセパレータのダスト排出口がはまるφ75mmのバカ穴と、ネジの下穴、
黄緑の同心円部分がバケツの縁がはまる溝。
内側から見た切削イメージのスクリーンショット
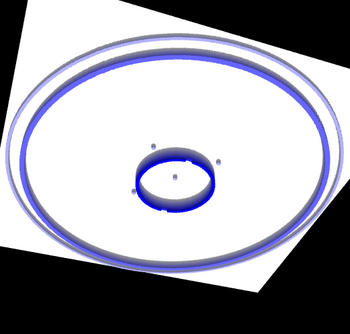
切削結果
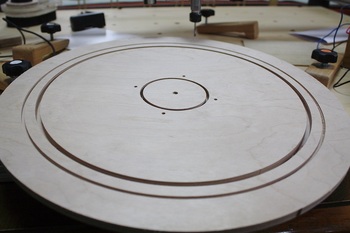
一番外側の溝は切り出し用の位置決め、その内側がバケツの縁が填まる溝で、
外径290mm深さ7mm、幅4mm
溝は、円周切ジグを使えばトリマーでもつくれそう。
溝外径はバケツの外径と全く同じからか、いずれかに僅かに変形があるのかもしれないが、いったんかちっとはまると蓋を持って少し振ったぐらいでは外れない。
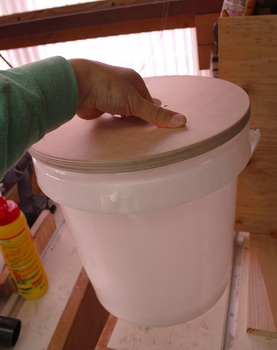
現状は、吸引する際の圧だけで密着しており、ロックやエアシールドは特に必要ない。
誤って蹴飛ばせば蓋が外れて塵が飛び散るというリスクはある。
次の問題は、サイクロンの吸い出し口とクリーナーの集塵ホースの繋ぎ。
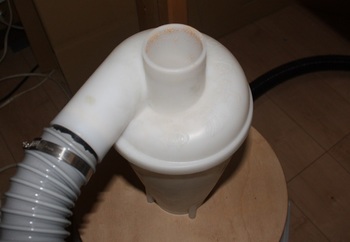
吸い出し口は内径50mm、外径55mmに対し、
クリーナーのホースは外径が35mm。市販の継ぎ手は見つかりそうになりので、
これもCNCで作る。
inkscapeでの作図。
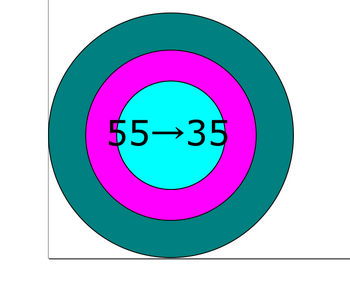
ピンクの外径が55mm、水色の外径が35mm、それぞれの円の内側をカットするGコードをJSCUTで作る。切削イメージのスクリーンショット。
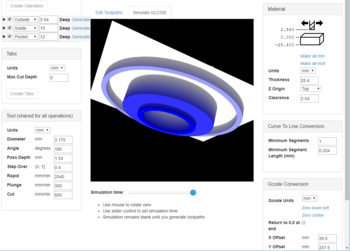
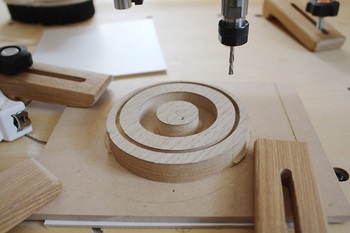
35mmのホールのみの部分の嵩を増すため板を継ぎ足す。
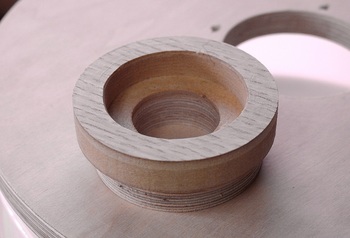
接続したところ
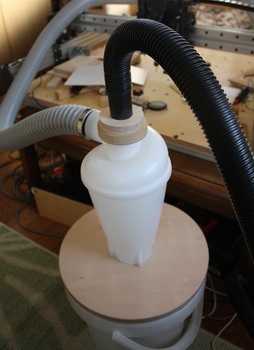
これはさすがみめんどくさいので、1年以上前だがCNC用の新しいサイクロンシステムを作る。
サイクロン部は中華製の既製品。
まず問題となるのは、サイクロン部と集塵容器部の接続・固定
集塵容器は、今までのサイクロンと同じ16L塗料容器を使う。
半透明で、ダストの溜まり具合が一目でわかるのがいい。
これにかぶせる木製蓋をCNCで切り出しサイクロン部を接合する
蓋の作図
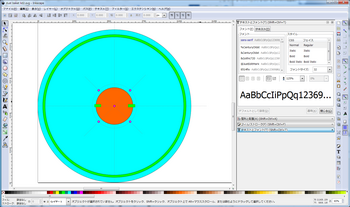
中心にセパレータのダスト排出口がはまるφ75mmのバカ穴と、ネジの下穴、
黄緑の同心円部分がバケツの縁がはまる溝。
内側から見た切削イメージのスクリーンショット
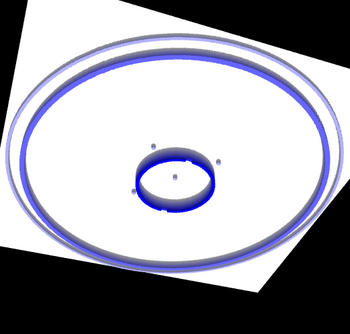
切削結果
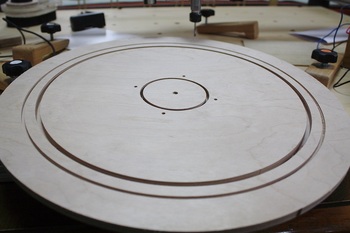
一番外側の溝は切り出し用の位置決め、その内側がバケツの縁が填まる溝で、
外径290mm深さ7mm、幅4mm
溝は、円周切ジグを使えばトリマーでもつくれそう。
溝外径はバケツの外径と全く同じからか、いずれかに僅かに変形があるのかもしれないが、いったんかちっとはまると蓋を持って少し振ったぐらいでは外れない。
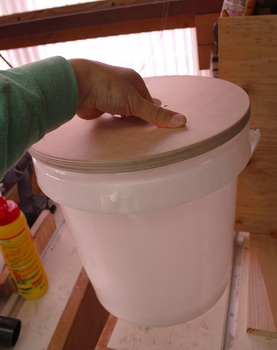
現状は、吸引する際の圧だけで密着しており、ロックやエアシールドは特に必要ない。
誤って蹴飛ばせば蓋が外れて塵が飛び散るというリスクはある。
次の問題は、サイクロンの吸い出し口とクリーナーの集塵ホースの繋ぎ。
吸い出し口は内径50mm、外径55mmに対し、
クリーナーのホースは外径が35mm。市販の継ぎ手は見つかりそうになりので、
これもCNCで作る。
inkscapeでの作図。
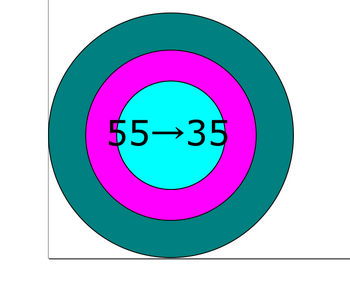
ピンクの外径が55mm、水色の外径が35mm、それぞれの円の内側をカットするGコードをJSCUTで作る。切削イメージのスクリーンショット。
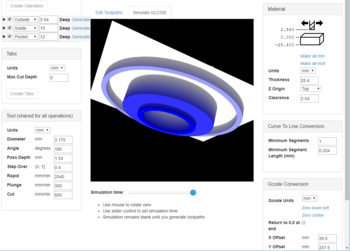
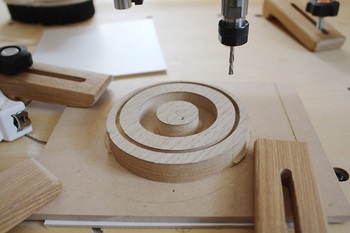
35mmのホールのみの部分の嵩を増すため板を継ぎ足す。
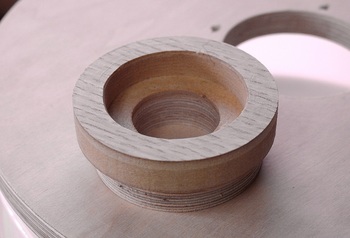
接続したところ
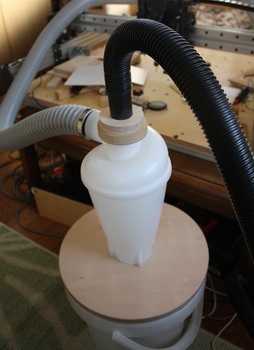
スタイロフォームを削る [CNC]
CNCで柔らか系の加工を試してみた。
スタイロフォームとは、発泡性の断熱材だが、
私の用途は、もっぱら大きいパネルを切断する際の下敷きに使用すること。
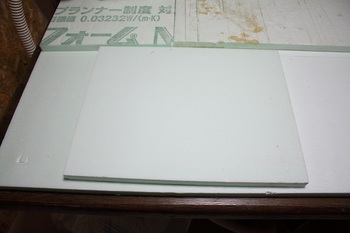
テーブルの上に置けば平面が出るのでたわみやすい材でも反ることはない。
丸鋸の刃を材の厚さより少しだけ出して一緒にフォームを切断してもブレードを痛めることもない。
そのため、しばらく使っているとフォームの面が切り溝だらけになる。
傷のついていない裏側を再利用すべく、CNCで削ってみた。
Inkscapeで作図
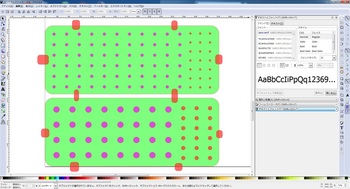
これをJSCUTでGコードにする。
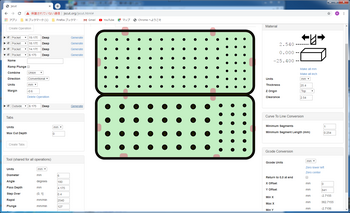
1パスの切り代(パスデプス)は、木材の場合だと堅木で1mm前後、
柔らかくてもせいぜい1.5mm程度だが、今回は6mmエンドミルを使ってパスデプスは4mm強とした。
セットして切削開始
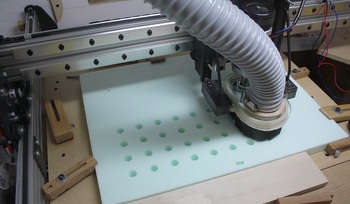
全くストレスがなく、パスデプス6mmでも問題ない感じ。
スタイロフォームは柔らか過ぎて、
ボール盤では材のぶれなどから切り口が荒れてうまくいかなかった。
切り口の荒れもこの程度であれば問題ない。
30分後
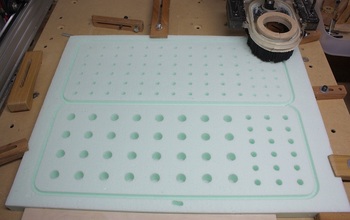
カッターで切り離し、外周はルーターで倣い切削
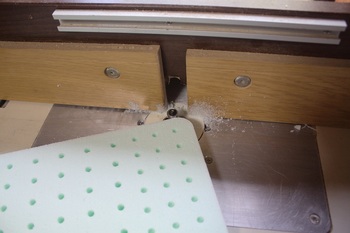
棚に両面テープで止めたところ。
スタイロフォームとは、発泡性の断熱材だが、
私の用途は、もっぱら大きいパネルを切断する際の下敷きに使用すること。
テーブルの上に置けば平面が出るのでたわみやすい材でも反ることはない。
丸鋸の刃を材の厚さより少しだけ出して一緒にフォームを切断してもブレードを痛めることもない。
そのため、しばらく使っているとフォームの面が切り溝だらけになる。
傷のついていない裏側を再利用すべく、CNCで削ってみた。
Inkscapeで作図
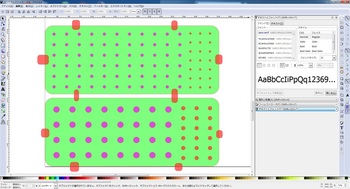
これをJSCUTでGコードにする。
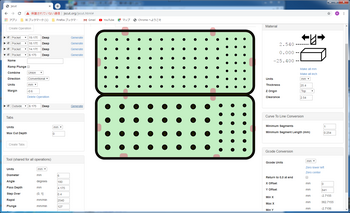
1パスの切り代(パスデプス)は、木材の場合だと堅木で1mm前後、
柔らかくてもせいぜい1.5mm程度だが、今回は6mmエンドミルを使ってパスデプスは4mm強とした。
セットして切削開始
全くストレスがなく、パスデプス6mmでも問題ない感じ。
スタイロフォームは柔らか過ぎて、
ボール盤では材のぶれなどから切り口が荒れてうまくいかなかった。
切り口の荒れもこの程度であれば問題ない。
30分後
カッターで切り離し、外周はルーターで倣い切削
棚に両面テープで止めたところ。
杉を接ぐ 後編 [木工]
スケッチアップによる完成形
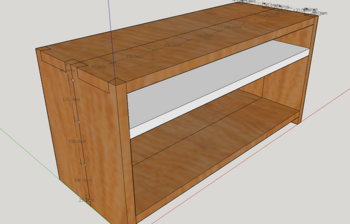
直角は蟻接ぎにする。
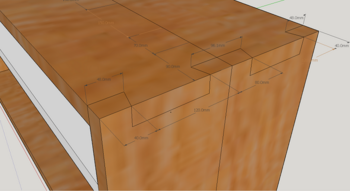
これが男木。
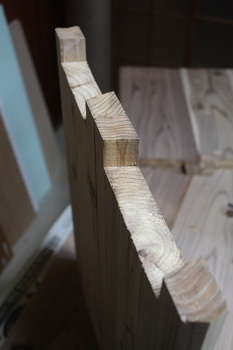
以前作ったバンドソー架台や本棚2号はバンドソーに傾斜したサブテーブル
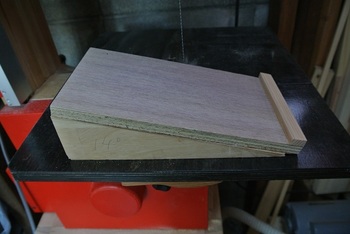
だけで作ったが、
今回は板幅が40cmで、バンドソーで懐が足りなくなる部分は、
手鋸で不要部分を切り取り、最後にノミで仕上げた。
男木を天板の接合面に置いて、現物あわせで罫書き線を入れて
切り取る。
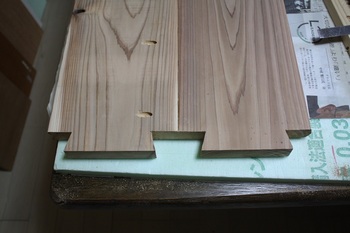
若干のみで整形しただけでほぼぴったり。
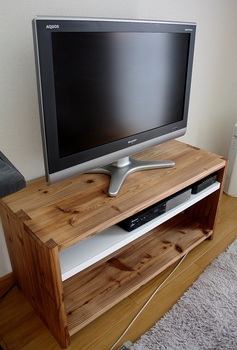
アリ接ぎは、接ぎそのものがデザイン上のアクセントになる。
中棚は、1×4を芯に両面に5mm合板を貼り、天面と前面にメラミン板を張り付けた。
棚部分の接合は、鉄製アングルの金具を両脚に付けて、それに棚を載せてねじ止めしただけ。
棚の木口面を金具の厚み分3mmほどトリマーで彫り込んで、
脚との間に隙間ができないようにしている。
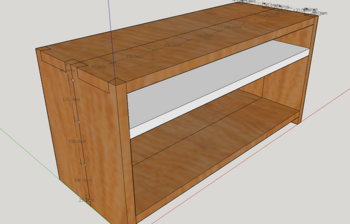
直角は蟻接ぎにする。
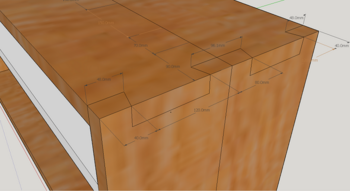
これが男木。
以前作ったバンドソー架台や本棚2号はバンドソーに傾斜したサブテーブル
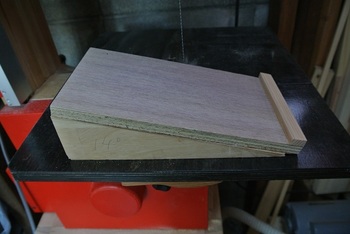
だけで作ったが、
今回は板幅が40cmで、バンドソーで懐が足りなくなる部分は、
手鋸で不要部分を切り取り、最後にノミで仕上げた。
男木を天板の接合面に置いて、現物あわせで罫書き線を入れて
切り取る。
若干のみで整形しただけでほぼぴったり。
アリ接ぎは、接ぎそのものがデザイン上のアクセントになる。
中棚は、1×4を芯に両面に5mm合板を貼り、天面と前面にメラミン板を張り付けた。
棚部分の接合は、鉄製アングルの金具を両脚に付けて、それに棚を載せてねじ止めしただけ。
棚の木口面を金具の厚み分3mmほどトリマーで彫り込んで、
脚との間に隙間ができないようにしている。
杉を接ぐ [木工]
杉は柔らかいので、もっぱら建築用という印象がある。
家具などのに使われることは少ないようだが、木目が美しい芯材の良質な杉板が目にとまり、創作意欲がわく。
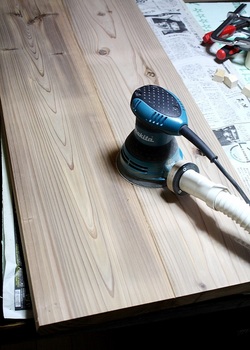
厚さ30mmとボリューム感もなかなか。
柔らかくて傷がつきやすいが、加工は楽だ。
幅が200mmなので、2枚をポケットホールジョイントとボンドで接ぐことにする。
ポケットホールジョイント用ジグは、こんな安物
を持っているが、何カ所も穴開けすると、クランプで取り付け・取り外しが面倒なので最近はほとんど使っていない。
で、最近のポケットホール開けはもっぱらこの方法。
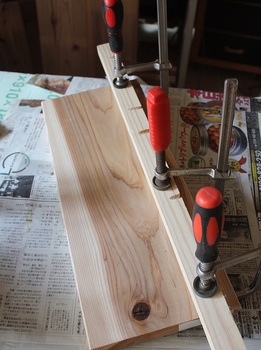
材に捨て板の角材をクランプで固定、材と角材の境目より少し角材側にフリーハンドで斜め穴を開けるだけ。角度の目安は15°程度。
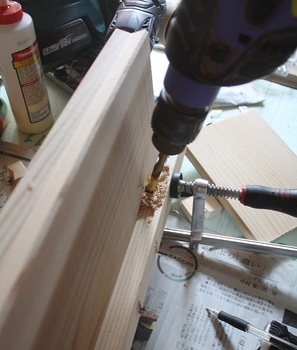
捨て板を付け替えることなく一気に一連のホールが作れる。
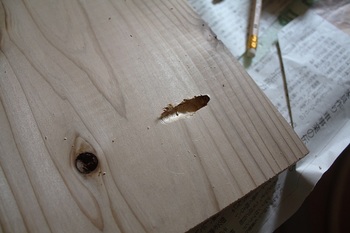
材の木端は、片側が山、反対が谷になっており、山と谷を合わせるだけで楽に羽目合わせできる。
最初、こんな保護材を木端の両側に固定、
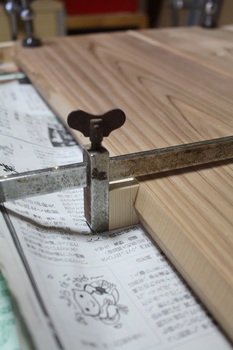
ボンドを接続面に塗布しハタガネで締めたが、ソリが出るため、各所の固定が必要になる。また、山・谷の中心がずれているせいで、接ぎ面に段差が生じてしまう。
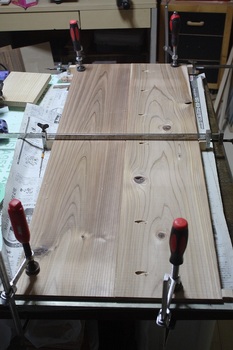
結局、2枚を平面に並べ、コースレットをネジ込んだ方がいいようだ。
これだと表面の段差や、締めによる反りも生じない。
ネジを入れたところ。
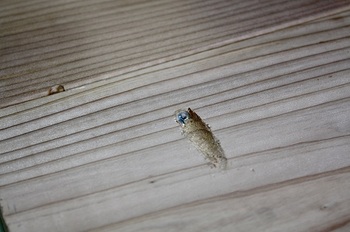
これにダボを挿し込み、はみ出した部分を切り取り、研磨すれば完璧なのだが、ホールは裏側や目につかない位置なので、今回は省略する。
ネジは65mmのコースレットを使用したが、ねじ込み角度が大きすぎると、反対側にネジの頭が出る。
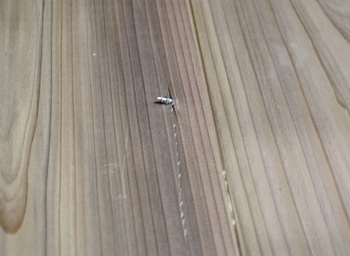
ここがフリーハンドの難しいところ。(^^ゞ
家具などのに使われることは少ないようだが、木目が美しい芯材の良質な杉板が目にとまり、創作意欲がわく。
厚さ30mmとボリューム感もなかなか。
柔らかくて傷がつきやすいが、加工は楽だ。
幅が200mmなので、2枚をポケットホールジョイントとボンドで接ぐことにする。
ポケットホールジョイント用ジグは、こんな安物
を持っているが、何カ所も穴開けすると、クランプで取り付け・取り外しが面倒なので最近はほとんど使っていない。
で、最近のポケットホール開けはもっぱらこの方法。
材に捨て板の角材をクランプで固定、材と角材の境目より少し角材側にフリーハンドで斜め穴を開けるだけ。角度の目安は15°程度。
捨て板を付け替えることなく一気に一連のホールが作れる。
材の木端は、片側が山、反対が谷になっており、山と谷を合わせるだけで楽に羽目合わせできる。
最初、こんな保護材を木端の両側に固定、
ボンドを接続面に塗布しハタガネで締めたが、ソリが出るため、各所の固定が必要になる。また、山・谷の中心がずれているせいで、接ぎ面に段差が生じてしまう。
結局、2枚を平面に並べ、コースレットをネジ込んだ方がいいようだ。
これだと表面の段差や、締めによる反りも生じない。
ネジを入れたところ。
これにダボを挿し込み、はみ出した部分を切り取り、研磨すれば完璧なのだが、ホールは裏側や目につかない位置なので、今回は省略する。
ネジは65mmのコースレットを使用したが、ねじ込み角度が大きすぎると、反対側にネジの頭が出る。
ここがフリーハンドの難しいところ。(^^ゞ
集塵フェンス製作の続き [CNC]
前回の、最後にある図形をGコード化し、シミュレートしたもの。
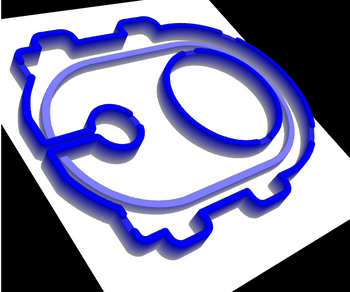
ちょうど材を切削が入る面の裏側からみたところで、タブの切り残しの具合がよくわかる。
このGコードで、アクリルを削る前に試し彫りしたMDF。
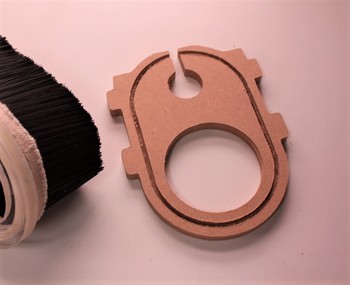
ブラシを嵌める溝に沿って、バンドソーで切断。
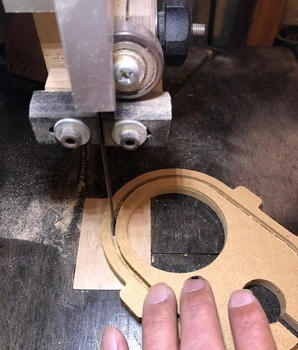
バンドソーの切り残しはフラシュビットで面取りして平滑にし、
最終的なブラシ高に合わせてスペーサーを接着。
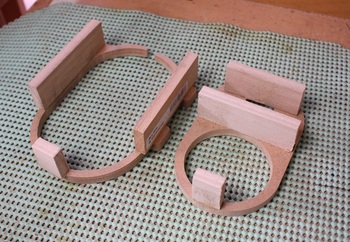
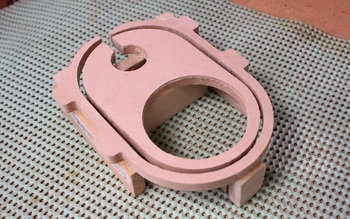
内側と外側の間のスペースにブラシを挟み込む。
挟み込んだところ。
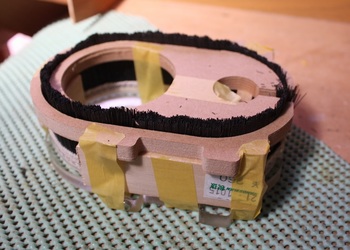
スペーサーの底はアクリルの面に置き、MDFのトップを基準面にブラシ高さを合わせる。
ブラシ部はAliexpressで購入したものだ、高さは7cmあったため、4cmに短くする。
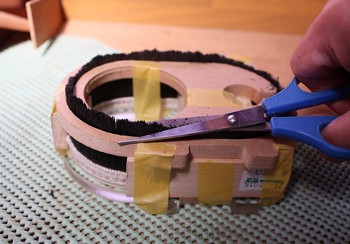
ハサミが紙用(^^;なのもあるが、ブラシは硬くてなかなか切れないし、平滑にするのは至難。
最後は、ベルトサンダーに押し付けてはみ出した部分を削り落とす。
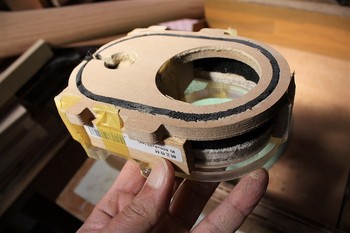
毛どうしが融着した部分もあるが、ほぐせば離れる感じ。
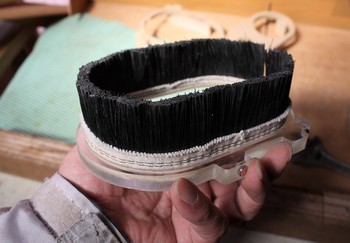
ブラシを底面を平滑にするこの方法は、以前youtubeのマリウス・ホルンベルガーの動画で見た方法だが、まあまあの出来栄えか。
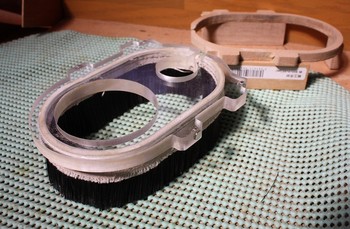
ここまで平滑にする必要があるかというのはある・・・
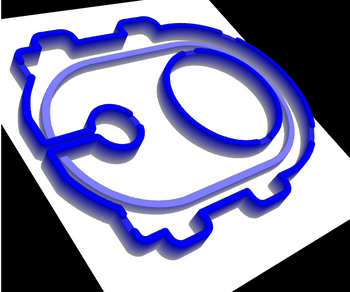
ちょうど材を切削が入る面の裏側からみたところで、タブの切り残しの具合がよくわかる。
このGコードで、アクリルを削る前に試し彫りしたMDF。
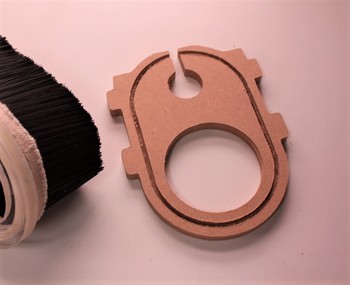
ブラシを嵌める溝に沿って、バンドソーで切断。
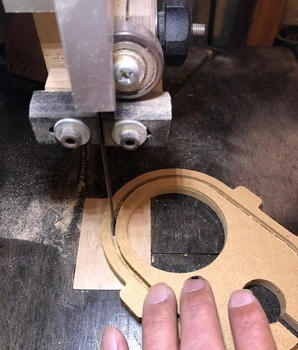
バンドソーの切り残しはフラシュビットで面取りして平滑にし、
最終的なブラシ高に合わせてスペーサーを接着。
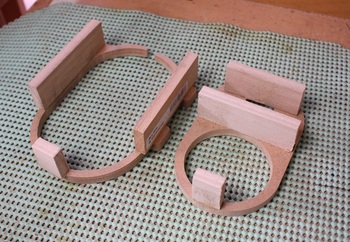
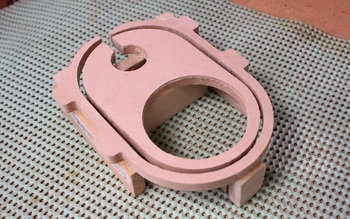
内側と外側の間のスペースにブラシを挟み込む。
挟み込んだところ。
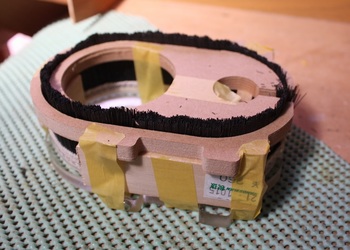
スペーサーの底はアクリルの面に置き、MDFのトップを基準面にブラシ高さを合わせる。
ブラシ部はAliexpressで購入したものだ、高さは7cmあったため、4cmに短くする。
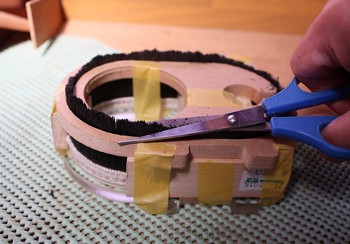
ハサミが紙用(^^;なのもあるが、ブラシは硬くてなかなか切れないし、平滑にするのは至難。
最後は、ベルトサンダーに押し付けてはみ出した部分を削り落とす。
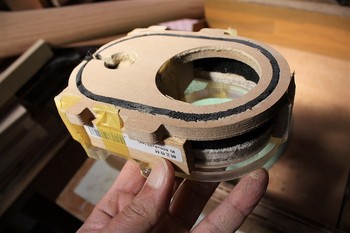
毛どうしが融着した部分もあるが、ほぐせば離れる感じ。
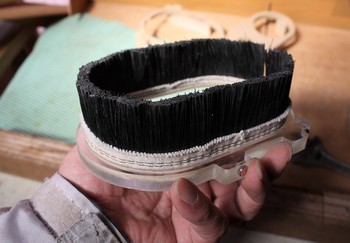
ブラシを底面を平滑にするこの方法は、以前youtubeのマリウス・ホルンベルガーの動画で見た方法だが、まあまあの出来栄えか。
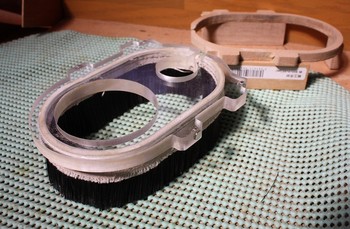
ここまで平滑にする必要があるかというのはある・・・
CNCでアクリルを削る。(CNC集塵対策) [CNC]
CNCで初めてアクリルを削ってみた。
ミルは木を削るときも使う1/8インチ径の2枚刃のスパイラル。
堅めの木の場合、パス当たりの切削深さは1.5mm、送り速度は毎分1000mmm程度にする事が多いが、アクリルはこれよりさらに堅いのでそれぞれ0.5mmと600mmに設定してみた。
パラメーターとしてスピンドルの回転数も考慮する必要があるが、もともと12000rpmまでしか回せないので、最高速度で問題なかろう。
削ったのは厚さ10mmのアクリル。
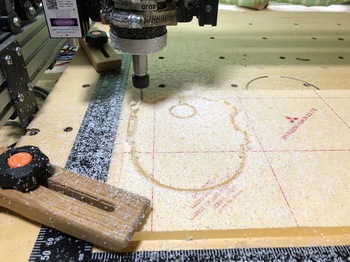
あっという間に削りカスだらけになる。
アクリルは比重もあり、粉になって舞い上がらないためこれでも扱いやすい。
木質材料の場合は、切りくずがかなり広範囲に広がって散らばるのと、粉塵が舞い上がるので、切削中はほぼ付きっきりで集塵機で吸い取る必要がある。
切削時間は約60分でこういうのができあがる。
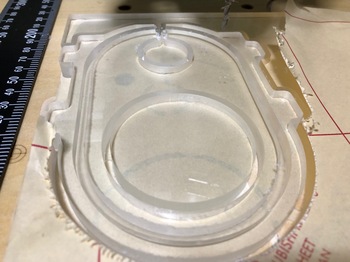
これが何かというとCNCルーターの集塵フェンスの天板部。
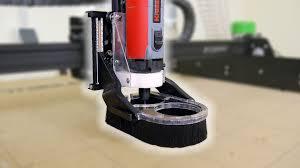
youtubeなどにある動画の英文では、よくdust shoe(「塵取り靴」?)と標記されている。
まあ、見た面はそんな感じもする。
6mmの深さで掘った溝にブラシをはめ込んで固定したところ。
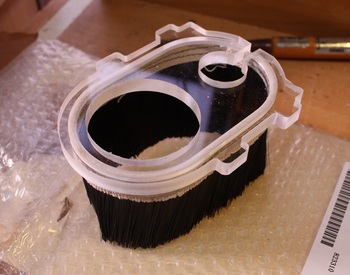
スリッパというよりデッキブラシに近い。
小さい穴にはエンドミルを通し、大きい方に集塵ホースが付く。
ちなみに、Gコード化(CAM)はJSCUTを使用したが、その前段でInkscapeでこういう図形を書いた。
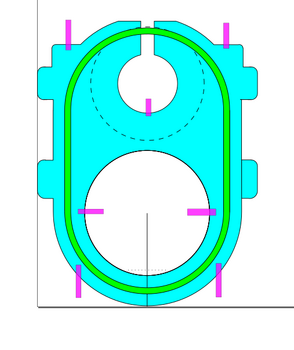
黄緑部分は幅4mmで、着諸部分を深さ6mmで削り、ブラシを嵌める溝にする。
水色部分は、これの外周を深さ10mmで切削し、外形を切り出す。
矩形のピンクはタブ(切り離した際に、パーツが動かいないように保持するため厚さ1.5mm程度の切り残し)を設定するためのもの。
こういう風に色分けし、それぞれの加工対象を図形化しておくとJSCUTの作業がやりやすい。
TV台を作る [木工]
個人的には、TVはほとんど見ないのだが、TV台はよく作る(笑)
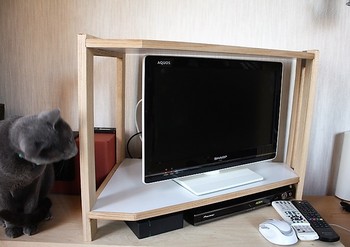
これは、要望があって作った娘のTV台。
低いキャビの上にTVやディスクプレーヤー、ハードディスクなどが占領していてなんともむさいので、これらを整理する意味合いもある。
最初は、オーソドックスにこういう設計をしてみたが・・・
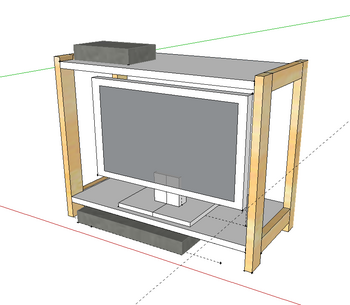
パーソナルスペースからのアクセスを考えると台の斜め方向からTVを見るか形になるため、こういう三角形状がものぐさ太郎には最適であることを発見する。
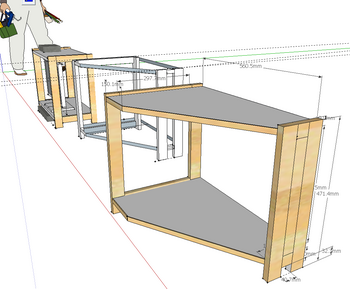
棚板は、40cm×90cmの化粧板を斜めに2分割して整形する。
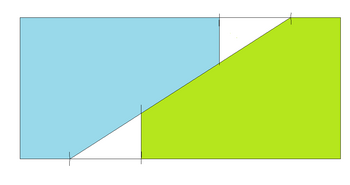
切断した木口には、フレームと同じ材種の薄板を貼りつける。
この棚の左右から5cm(4cm)×2cm断面の角材を組み合わせたフレームを作り、両側から挟み込んで、スクリューで止める。
角材の接合は、簡易にダボ組とする。
通常、ダンボ穴開けにはこういう治具が便利でよく使っているが、
治具の2本のポールで材を挟み込んで中心・垂直出しをする関係で、小さい木口断面や木端の端への穴開けには使いずらい。
そこで、フレームにする角材の一部を切り取って、こういう感じに穴を開けた治具を作る。確か、Youtubeのマリウス・ハンベルガーのチャンネルで見たテクニックだ。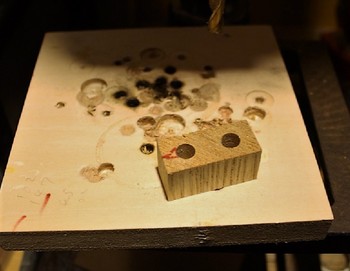
木口には、こういう感じに重ねてクランプで固定し、穴をガイドにしてドリルで穴を空ける。
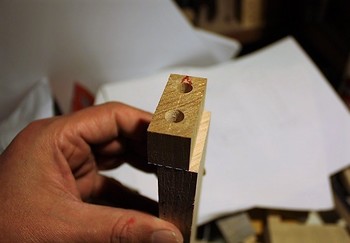
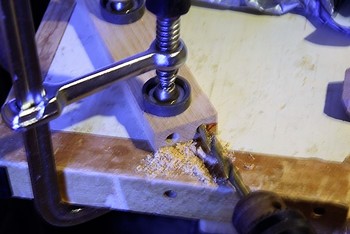
もとは同じ材、同じサイズになるので、位置決め精度は文句なし。
相方の木端にも同じ治具をクランプで固定し、ドリルを通す。
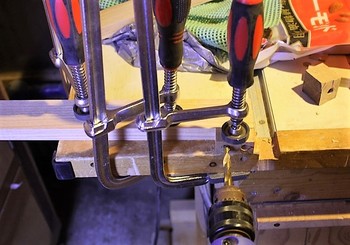
写真をあまり撮っていなかったので分かりずらいが、組む相方の方向をよく考えて治具を当てないとうまく接合できない。
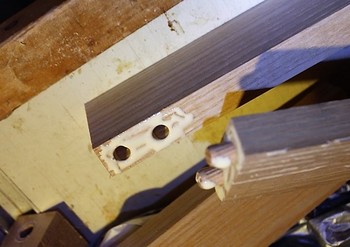
で、できたのがこれ。
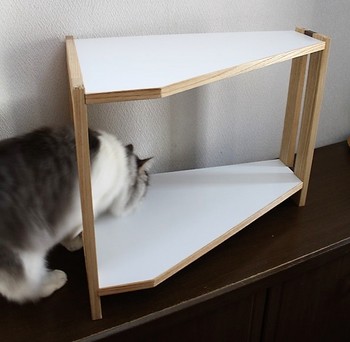
猫はなかなか好奇心旺盛です。
フレーム側には、棚を落とし込むために、ルーターで2~3mm程度の溝を掘っている。
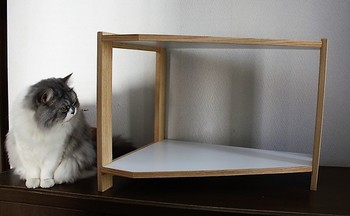
猫が邪魔して下の方が見えないが、
狭い方のフレームの横方向を繋ぐ材はウォールナット。
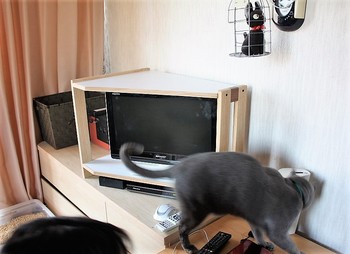
濃い色をワンポイントにして少しカッコよさを狙った。
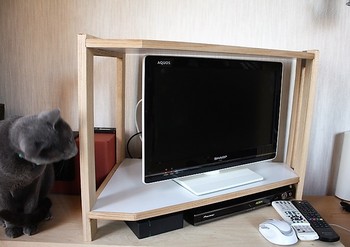
これは、要望があって作った娘のTV台。
低いキャビの上にTVやディスクプレーヤー、ハードディスクなどが占領していてなんともむさいので、これらを整理する意味合いもある。
最初は、オーソドックスにこういう設計をしてみたが・・・
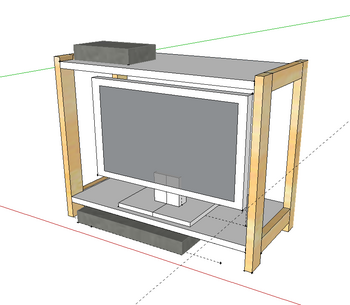
パーソナルスペースからのアクセスを考えると台の斜め方向からTVを見るか形になるため、こういう三角形状がものぐさ太郎には最適であることを発見する。
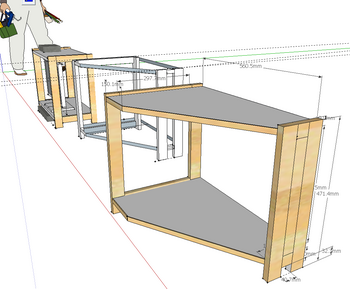
棚板は、40cm×90cmの化粧板を斜めに2分割して整形する。
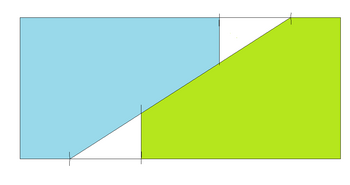
切断した木口には、フレームと同じ材種の薄板を貼りつける。
この棚の左右から5cm(4cm)×2cm断面の角材を組み合わせたフレームを作り、両側から挟み込んで、スクリューで止める。
角材の接合は、簡易にダボ組とする。
通常、ダンボ穴開けにはこういう治具が便利でよく使っているが、
治具の2本のポールで材を挟み込んで中心・垂直出しをする関係で、小さい木口断面や木端の端への穴開けには使いずらい。
そこで、フレームにする角材の一部を切り取って、こういう感じに穴を開けた治具を作る。確か、Youtubeのマリウス・ハンベルガーのチャンネルで見たテクニックだ。
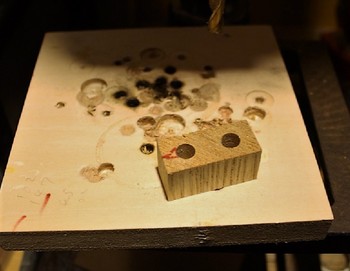
木口には、こういう感じに重ねてクランプで固定し、穴をガイドにしてドリルで穴を空ける。
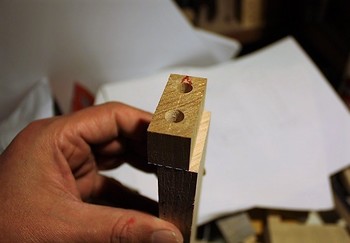
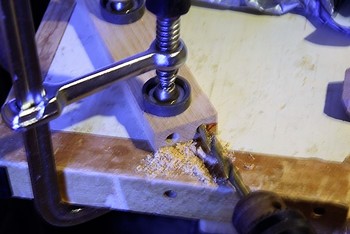
もとは同じ材、同じサイズになるので、位置決め精度は文句なし。
相方の木端にも同じ治具をクランプで固定し、ドリルを通す。
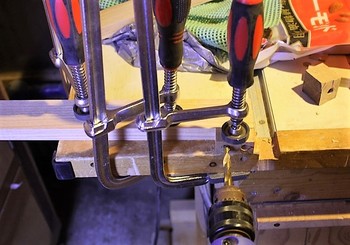
写真をあまり撮っていなかったので分かりずらいが、組む相方の方向をよく考えて治具を当てないとうまく接合できない。
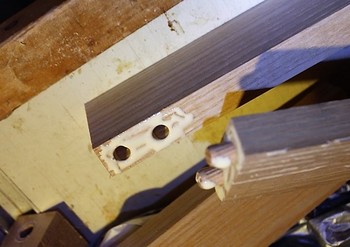
で、できたのがこれ。
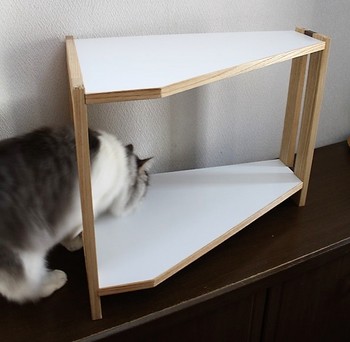
猫はなかなか好奇心旺盛です。
フレーム側には、棚を落とし込むために、ルーターで2~3mm程度の溝を掘っている。
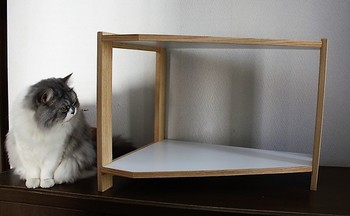
猫が邪魔して下の方が見えないが、
狭い方のフレームの横方向を繋ぐ材はウォールナット。
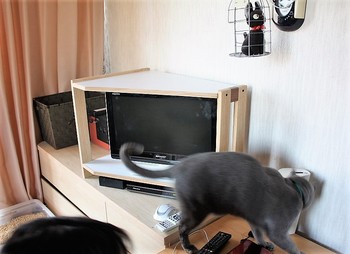
濃い色をワンポイントにして少しカッコよさを狙った。
IQランプを作る
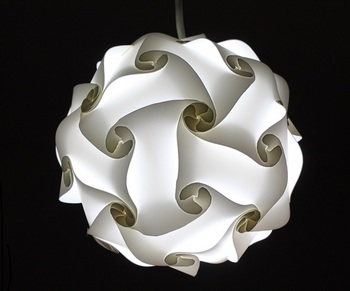
なかなか幻想的な写真。
前回に引き続き照明系です。
照明を消すとこんな具合
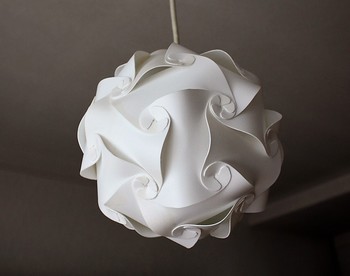
まったく表情が変わって面白い。
これ、IQランプ(IQ lamp)というランプシェードです。
左の一灯式ペンダントのシェードを取って、ランプだけを中に入れている。
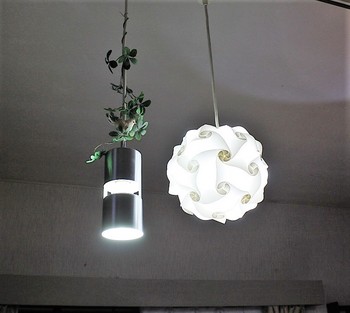
こういう形状のシート30枚を組み合わせて作る。
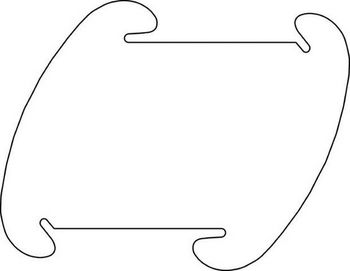
このシートをレーザーカッターで切り出すべく、習作のつもりでずいぶん前から作り始めていたがようやく完成した。
素材は、ポロプロピレンのシート
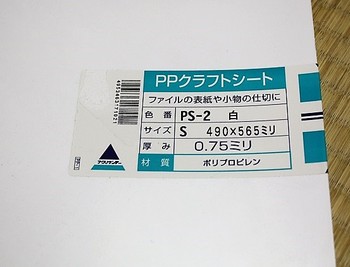
厚さが0.75mmもあって、実はもっと薄いほうがよかった。
これに30枚のシートが無駄なく収まるようCADを作成。
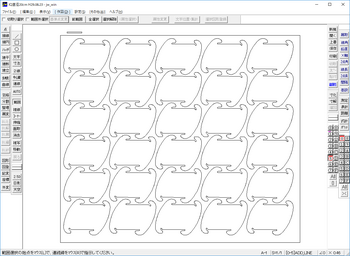
このサイズだと出来上がりは20cmになる。
ここからが結構大変。曲線の集合なのでデータが重い重い。
インクスケープで図形の一部を見たところ・・・・細かすぎる。
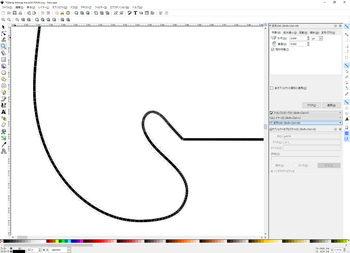
データを間引くべきだったが、当時は方法がわからずそのままGコードを作る。
が、重たすぎるので一行、5枚のみのをカットするGコードにし、
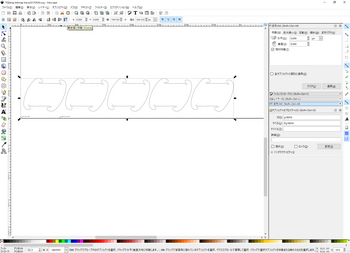
1行終わるごとに、シート現物かY軸原点を75mmづつ動かすことにする。
しかし、0.5Wの半導体レーザーでは全く歯が立たず。
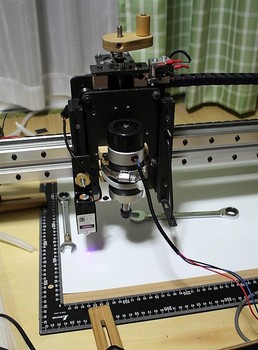
5cm/分で送ってもレーザーが当たった部分に溝はできるが、切れる気配がない。それでもこの速度だと1行5ピースの加工に50分近くかかってしまう。
結局、最後はハサミやカッターで切り刻み、切れ込みの先端部分はボール盤で3.5mmの穴をあけた。
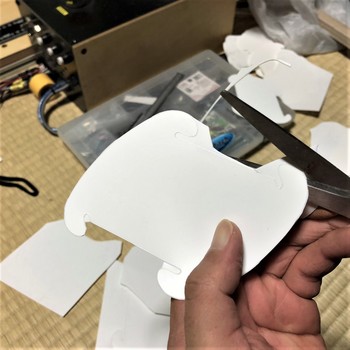
途中中断もあったりで、完成までになんと半年!
で、アマゾンを見ると40cmのものがこの値段。
IQランプが欲しいだけなら買った方がはるかにお得です。
バンドソーにLED照明を付ける [バンドソー]
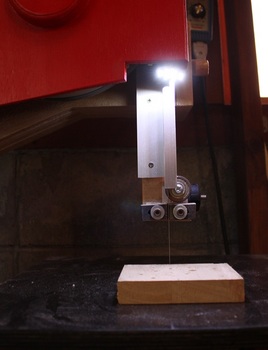
工房にはまともな照明がないため、
バンドソーの手元照明は当初からか付けたいと考えてきたのだが、なかなか手がつかず。
100円ショップで買ったボタン電池式でクリップのついたやつや、
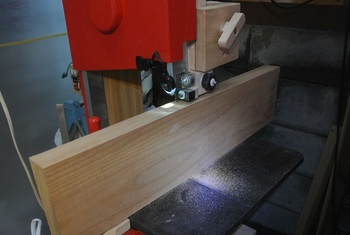
フックのついた電池式LEDなどを吊るして使っていたが、
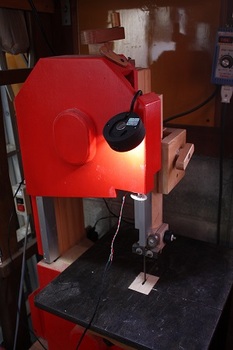
今回、ようやくLEDモジュールを使ってコンパクトなバンドソースイッチ連動式の手元照明を付ける。
実際に使ったのは、秋月電子で購入したLEDモジュール
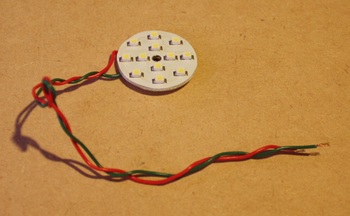
抵抗はすでに仕込んであるので、12V電源を繋ぐだけで点灯する。
消費電力は、確か50mA程度だったと思う。
裏側に電極があり、自分でケーブルをハンダ付けした。
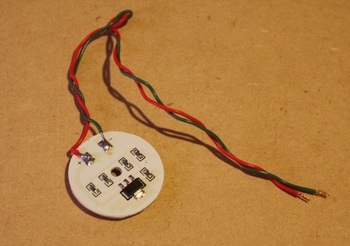
中心に空いた穴に小径の造作ねじを通し、プラスペーサーを間に挟んで直接ホイールカバーの裏側にねじ込む。
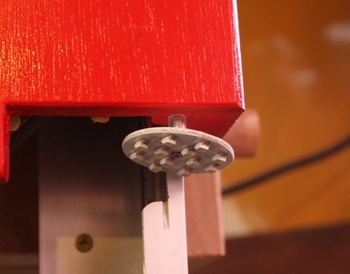
かなりいい加減なカバー裏の配線。
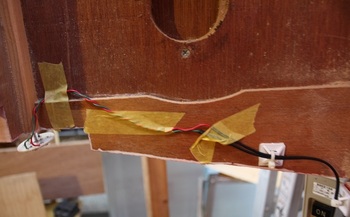
DC12Vを供給するACアダプタは、バンドソー(ACアダプタの上の黒い丸型コンセントがモーターのもの)と共通のコンセント刺さっており、ここへのAC100V給電を主電源スイッチにより行う。
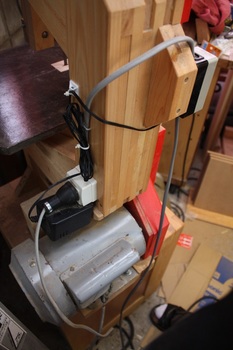
ACアダプタは相当に古い9Vだが、特に暗いとかの不都合はない感じだ。
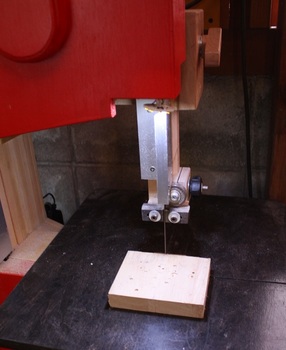
CNCで木製ノブを作る(その3) [工具]
Gコードを実行する。
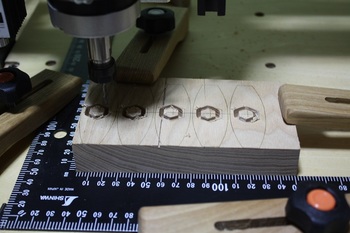
結果がこれ。
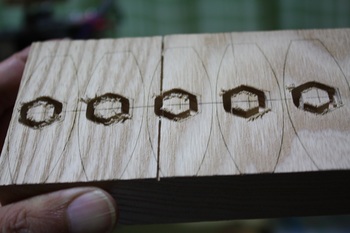
レーザーの線に対して1,2mm左側にずれている。
プローブの際にフェンスに当てたエンドミルは2枚刃のスパイラル形状のため、当たったときの位置関係によっては誤差が生じた可能性、あるいは、材が右側に動いた可能性もある。
ここは、線の方を修正すべく、レーザーの罫引き線を引き直す。
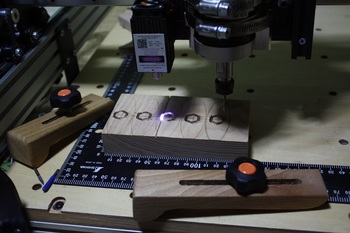
まだ少しずれている感じで修正量が少なかったようだが、ここはあまり精度は必要ないのでこれでよしとする。
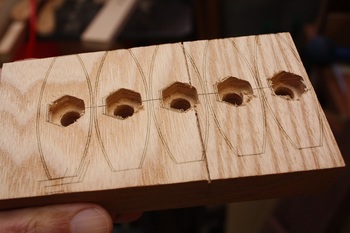
バンドソーでカット
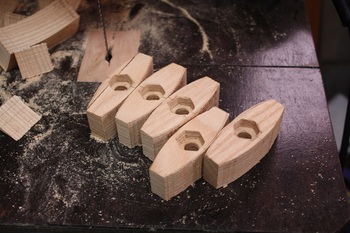
さらに、羽の両サイド裏側をカット。
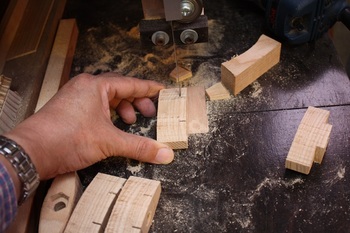
ナットを押し込んだとろこ。
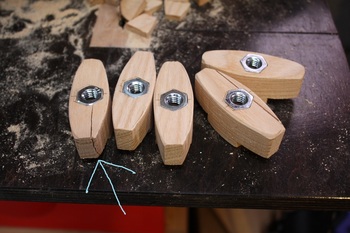
CNC加工部分は毛羽立ちをカッターで削った程度でとくに修正は行わなかったが、ナットの面取りしてある方を下にハンマーで叩くとすんなり入った。
抜ける心配はなさそうだが、必要ならエポキシで接着すればいい。
矢印に割れが入っているが、材が木口に面した端材で元からあったひびが広がったようだ。
ボンドを入れて、ネジ止めして修復。
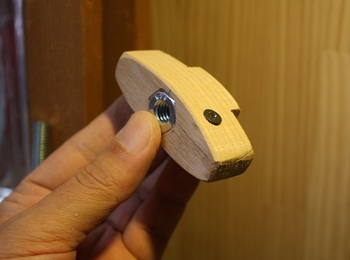
ノブスタートの比較
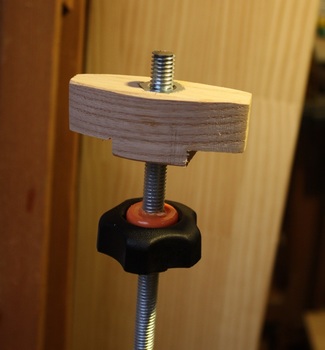
径が大きいので、当然締めのトルクも強い。
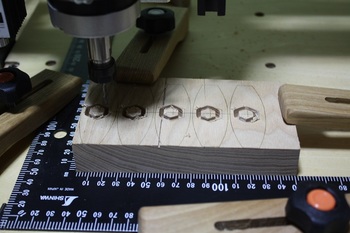
結果がこれ。
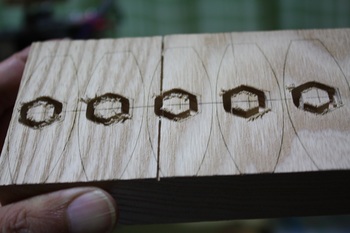
レーザーの線に対して1,2mm左側にずれている。
プローブの際にフェンスに当てたエンドミルは2枚刃のスパイラル形状のため、当たったときの位置関係によっては誤差が生じた可能性、あるいは、材が右側に動いた可能性もある。
ここは、線の方を修正すべく、レーザーの罫引き線を引き直す。
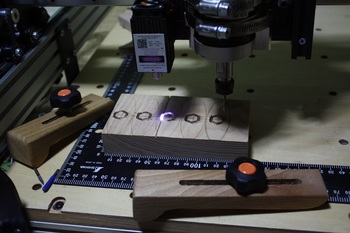
まだ少しずれている感じで修正量が少なかったようだが、ここはあまり精度は必要ないのでこれでよしとする。
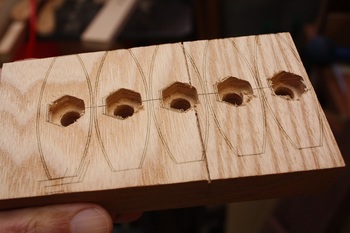
バンドソーでカット
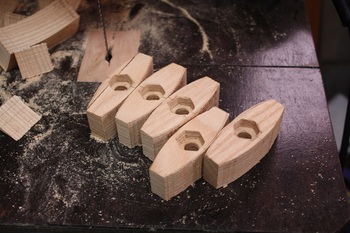
さらに、羽の両サイド裏側をカット。
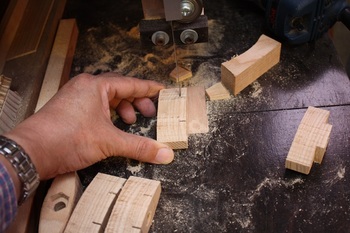
ナットを押し込んだとろこ。
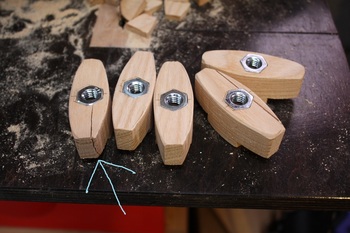
CNC加工部分は毛羽立ちをカッターで削った程度でとくに修正は行わなかったが、ナットの面取りしてある方を下にハンマーで叩くとすんなり入った。
抜ける心配はなさそうだが、必要ならエポキシで接着すればいい。
矢印に割れが入っているが、材が木口に面した端材で元からあったひびが広がったようだ。
ボンドを入れて、ネジ止めして修復。
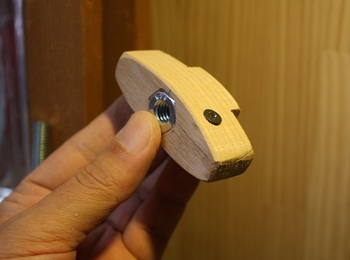
ノブスタートの比較
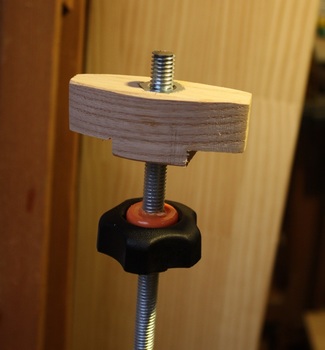
径が大きいので、当然締めのトルクも強い。