バンドソー(その5)モーターマウントとブレードガイド [バンドソー]
フレームの底、モーターマウント部は、下のシャフトホルダ部を取り付けてからの作業となる
廃材利用を前提にしているためか?この部分にこういう積層が必要かという疑問があるが、
板を順番に張り付けるだけなので、簡単と言えば簡単。
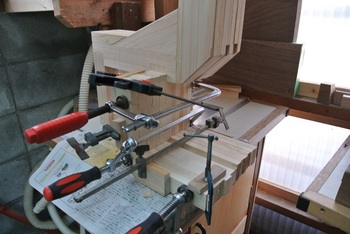
安易にやっていると、そこに落とし穴が・・・フレーム全体が前かがみのような気がして、定規を当ててみると。
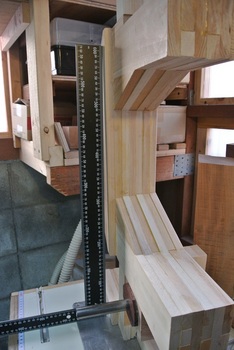
簡単な作業と緊張感が緩んだからか、フレームの直立確認を漏らしてしまっていた。
底には下駄をはかせる予定なので、そこで調節すればいいのだが、そこに行き着くまで、このバンドソーで切り出すので、もう少し直立させようと底を手カンナで削るはめに。
う~ん、なんともこういう局面が多い(^^;
これにモーターを置いて、回してみる。
ちなみにテーブルは、本テーブルを作るまでの一時テーブルで傾斜はできない。
刃がむき出しのため慎重に切断してみる・・・
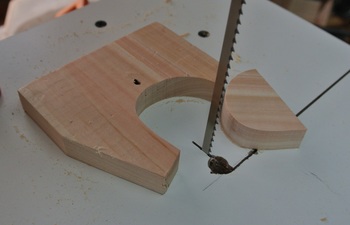
思った以上にサクサクと切れる。それも、丸鋸やジグソーのように大袈裟な音を出さないところがよい。電源を入れるのがストレスにならない。
このままではおっかないので、ひとまずブレードガイドを付けることに。
ブレードガイドはそれほど難しくない。
左が上ガイド、右が下ガイド
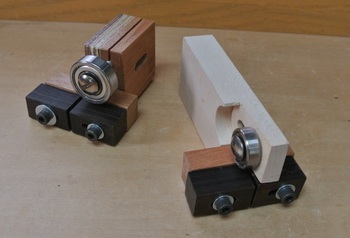
この部分はスケールダウンがなく、サイズはほとんどオリジナルと同じ。
ただし、下ガイドは、全体のスケールダウンの影響でオリジナルと同じ配置ではうまく収まらないため、設計変更して本来ベアリングとブレード押さえの位置を上下を逆にしていた。それをすっかり忘れてしまい、できあがった上の写真ではベアリングとその支持部が左右逆の位置に付いている。
これが設計変更のブレードガイドの正面。
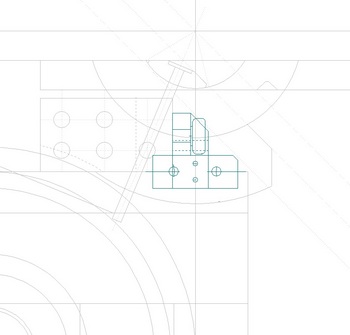
テーブル傾斜がなければこれでも問題ないので、ひとまずこのまま使うことに。
ブレードを左右から挟むブロックは、たまたまホームセンターで目にした黒檀を使用。
これに開けるスライド用の長穴はルーターテーブルで予想外に簡単できた。
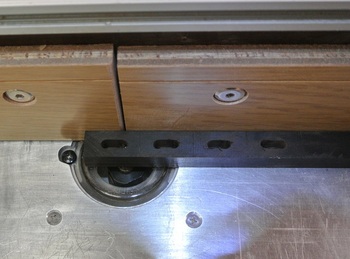
長棒のまま5mm穴を2箇所×4個=8個開け、5mmのエンドミル
をこれに挿し
裏表からそれぞれルーターテーブルのフェンスに沿って隣の穴までスライドさせる。
最後に必要な長さに切断。
台座の桜材に開けた穴の途中までタップを切り、これをM5ボルトをねじ込んでブロックを固定。
オリジナルはM6だが、黒檀ブロックのサイズが小さいため、ここだけサイズダウンする。
一時使用の場合の下ブレードガイドの配置箇所
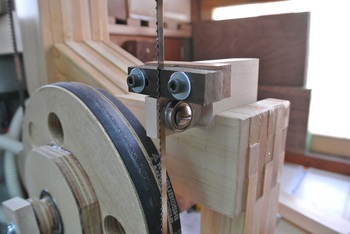
下ブレードガイドは、最終的にはフレームの上に載せるテーブルの台座にボルトで固定し前後にスライドするのだが、ここでは一時使用なので左右から一時台座に挟み込むことに。力をかけて押せば前後に動くがブレる心配は無い。
上ブレードガイド 左側から
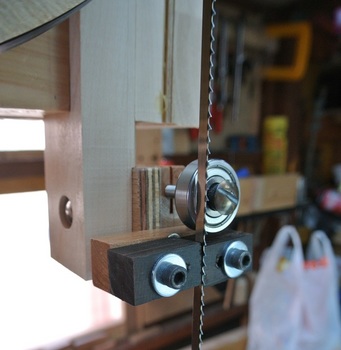
上ブレードガイドを固定するアームを上下にスライドさせガイドの高さを決める。
固定は、アーム裏側に埋め込んだむ角根ボルト
に通して前後にスライドする。
また、このボルトはブレードの後ろを支持するベアリングの位置固定も兼ねる。
上ブレードガイド 右側から
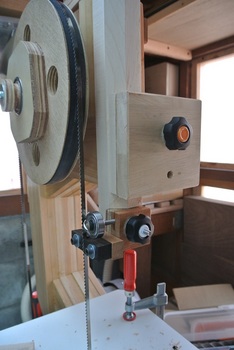
アームは右側にあるボルトでフレームに押しつけて固定。
アームが当たるフレームの切り欠き。
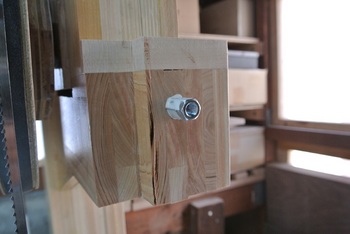
切り欠きの縦のラインに沿ってアームが上下するので、実際にホイール、刃を取り付けて位置決めした後に、刃と平行になるように丸鋸で切除する。
最後に重要な精度出しをするので、フレームの上メンバーなどは長めでさえあればあとはなんとかなるのだが、
今回メンバー長をぎりぎりにしたせいでアームの背が当たる部分の幅が狭くなり過ぎた。
ブレードガイドを付けて試し切り。
刃のブレが減ったせいか切り口がかなりなめらかになった。
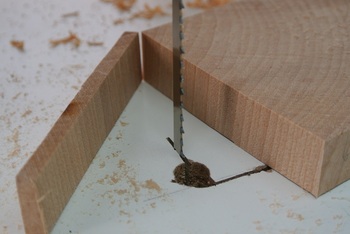
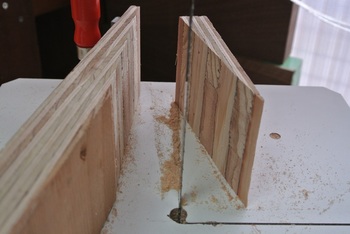
廃材利用を前提にしているためか?この部分にこういう積層が必要かという疑問があるが、
板を順番に張り付けるだけなので、簡単と言えば簡単。
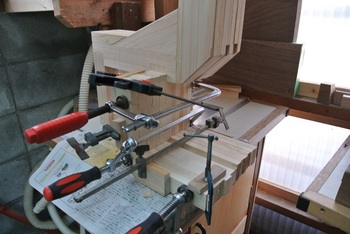
安易にやっていると、そこに落とし穴が・・・フレーム全体が前かがみのような気がして、定規を当ててみると。
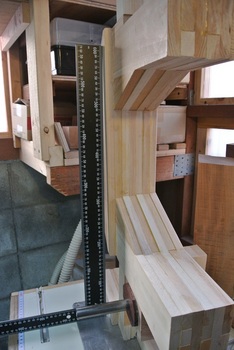
簡単な作業と緊張感が緩んだからか、フレームの直立確認を漏らしてしまっていた。
底には下駄をはかせる予定なので、そこで調節すればいいのだが、そこに行き着くまで、このバンドソーで切り出すので、もう少し直立させようと底を手カンナで削るはめに。
う~ん、なんともこういう局面が多い(^^;
これにモーターを置いて、回してみる。
ちなみにテーブルは、本テーブルを作るまでの一時テーブルで傾斜はできない。
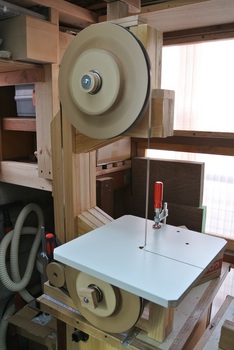
刃がむき出しのため慎重に切断してみる・・・
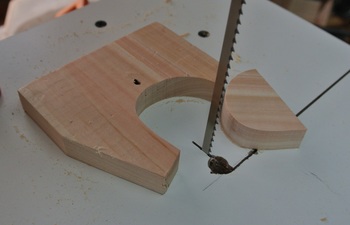
思った以上にサクサクと切れる。それも、丸鋸やジグソーのように大袈裟な音を出さないところがよい。電源を入れるのがストレスにならない。
このままではおっかないので、ひとまずブレードガイドを付けることに。
ブレードガイドはそれほど難しくない。
左が上ガイド、右が下ガイド
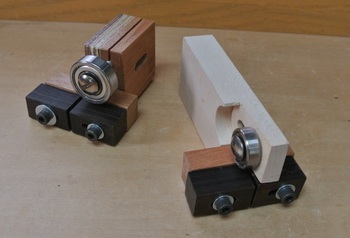
この部分はスケールダウンがなく、サイズはほとんどオリジナルと同じ。
ただし、下ガイドは、全体のスケールダウンの影響でオリジナルと同じ配置ではうまく収まらないため、設計変更して本来ベアリングとブレード押さえの位置を上下を逆にしていた。それをすっかり忘れてしまい、できあがった上の写真ではベアリングとその支持部が左右逆の位置に付いている。
これが設計変更のブレードガイドの正面。
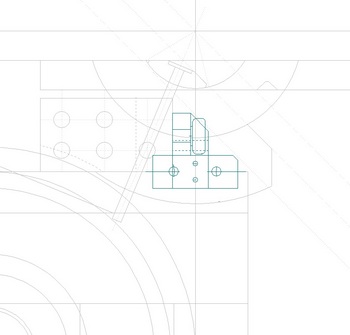
テーブル傾斜がなければこれでも問題ないので、ひとまずこのまま使うことに。
ブレードを左右から挟むブロックは、たまたまホームセンターで目にした黒檀を使用。
これに開けるスライド用の長穴はルーターテーブルで予想外に簡単できた。
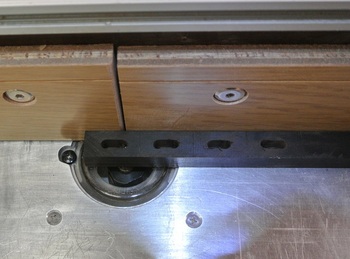
長棒のまま5mm穴を2箇所×4個=8個開け、5mmのエンドミル
裏表からそれぞれルーターテーブルのフェンスに沿って隣の穴までスライドさせる。
最後に必要な長さに切断。
台座の桜材に開けた穴の途中までタップを切り、これをM5ボルトをねじ込んでブロックを固定。
オリジナルはM6だが、黒檀ブロックのサイズが小さいため、ここだけサイズダウンする。
一時使用の場合の下ブレードガイドの配置箇所
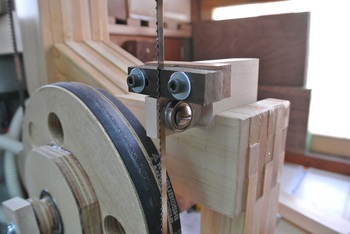
下ブレードガイドは、最終的にはフレームの上に載せるテーブルの台座にボルトで固定し前後にスライドするのだが、ここでは一時使用なので左右から一時台座に挟み込むことに。力をかけて押せば前後に動くがブレる心配は無い。
上ブレードガイド 左側から
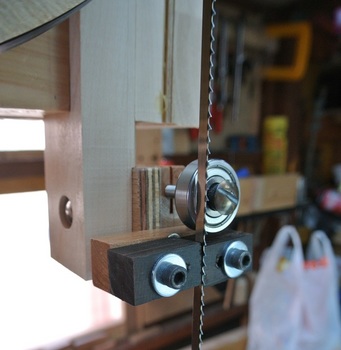
上ブレードガイドを固定するアームを上下にスライドさせガイドの高さを決める。
固定は、アーム裏側に埋め込んだむ角根ボルト
また、このボルトはブレードの後ろを支持するベアリングの位置固定も兼ねる。
上ブレードガイド 右側から
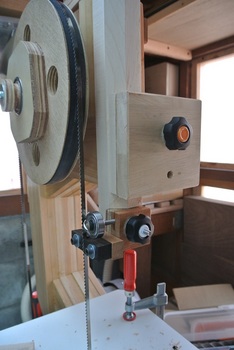
アームは右側にあるボルトでフレームに押しつけて固定。
アームが当たるフレームの切り欠き。
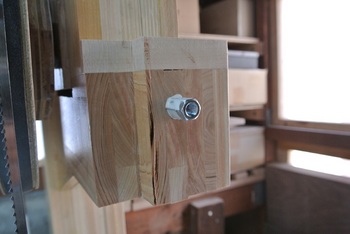
切り欠きの縦のラインに沿ってアームが上下するので、実際にホイール、刃を取り付けて位置決めした後に、刃と平行になるように丸鋸で切除する。
最後に重要な精度出しをするので、フレームの上メンバーなどは長めでさえあればあとはなんとかなるのだが、
今回メンバー長をぎりぎりにしたせいでアームの背が当たる部分の幅が狭くなり過ぎた。
ブレードガイドを付けて試し切り。
刃のブレが減ったせいか切り口がかなりなめらかになった。
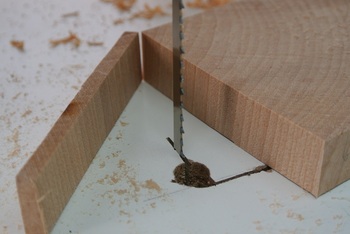
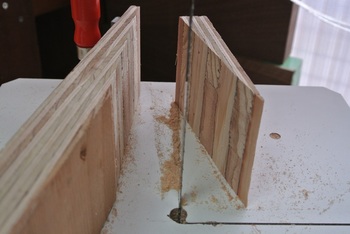
バンドソー(その4)シャフトホルダーまわり [バンドソー]
ホイールはやたら手間暇がかかったが、
シャフトホルダーはそれに輪をかけて難関。
はっきり言って、バンドソーがあったほうがよい(笑)。
これが上ホイール用シャフトホルダの素材となる桜の端材ブロック。
プレーナーが掛かっているのは接する2面のみ。その直角も怪しい。
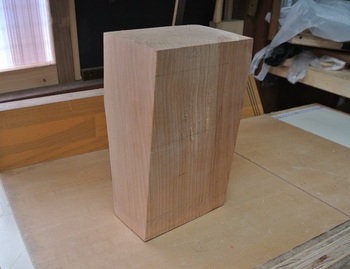
元はこの倍の幅があったのだが丸鋸で縦に挽き割って2分割にし、もう一方を下ホール用に。
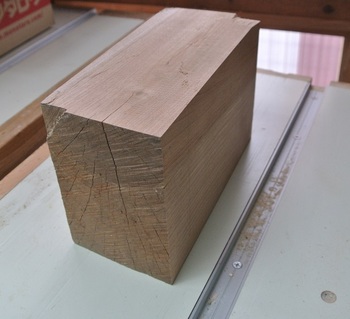
挽き割ると言っても、丸鋸なので裏表からせいぜい3cmづつ、少しづつ刃を入れる。裏表の平行が十分に出ていないため、切り口に段差ができる。せめて自動かんな等でちゃんとした面が出せればよかったのだが。
最大の鬼門はシャフトを通す20mmの長穴開け。
手持ちのフォスナービットと卓上ボール盤では、途中でテーブルをかさ上げしても60~70mmの深さがせいぜい。
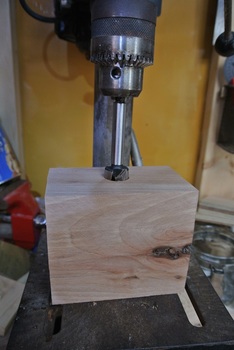
そこからは鉄工用のロングビットを使ってガイド穴を開け、
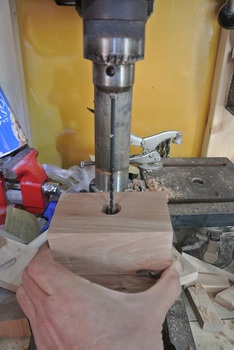
裏面からこのガイド穴を頼りに再度フォスナーで貫通穴を開けたが・・・・結果はこのとおり。
やは穴の接続箇所に段差が出来た。
素直にロングビット
やこういうカッター
を入手すべきだったと後悔。
フォスナービットを突っ込んで段差を消したが、 シャフトを入れてみると途中から急にきつくなり、ハンマーで叩いてみるがほとんど動かない。時すでに遅し(^^;)。抜くに抜けず、ハンマーでたたくに叩いて、なんとかこの位置で押し込んだ・・・シャフトを抜くためにはブロック全体を破壊するしかない。
まあ、これで絶対に抜ける心配はない。
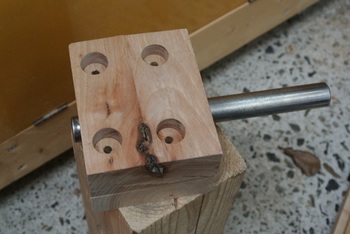
そのうえ、 対面の平行が出ていないのに無造作に両面から穴明けしたせいだろうが・・・・
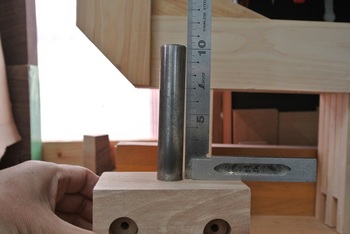
幸いしたのは、シャフト傾きは固定するフレーム前面に対して左右方向のため、ブロックを少し左に振って固定するだけでよい。
上下の傾きだとフレームとホルダーの間に薄板シムを入れて調整しなければならなくなる。
そして、これが上ホルダ。このシャフトも同じく抜けません(笑)
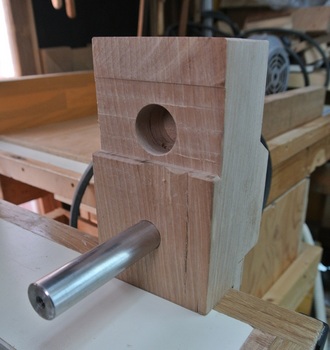
切り欠きが多く、それぼどの精度必要でないので、バンドソーがあれ楽勝なのだが、丸鋸テーブルとルーターで難儀したせいで思いっきり汚い仕上げ(^^;)
シャフトの上の穴には、ホルダーブロックの上から貫通穴を通したボルトを入れ、内部にこの叩いて曲げたワッシャ
とナットで帯鋸刃のテンションを調節する。
上ホルダ裏側には、上ホイールの前後の傾きを調節するM10ボルトを小さめの穴にねじ込む。この後、ボルトヘッド部分はグラインダーで切除。

下のホルダーは径6mm、長さ90mmの長ネジでフレーム下部に固定、上はフレーム頂きの二つの突起の間に載せ、ボルトで上に引っ張る。
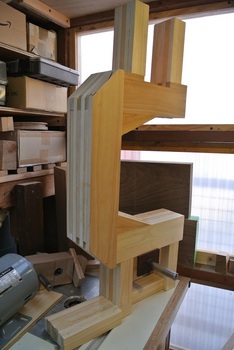
シャフトにホイールを通し、帯鋸刃を掛けてトラッキングの具合を確認する。
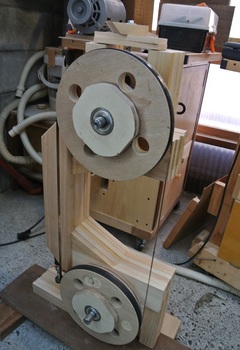
大体の場合うまくいくのだが、クラウンの角度がありすぎるせいか、時としてトラックの中心まで登り切れない場合がある。
クラウンの傾斜を緩くするよう切削したところ、しっかりとトラッキングするようになった。
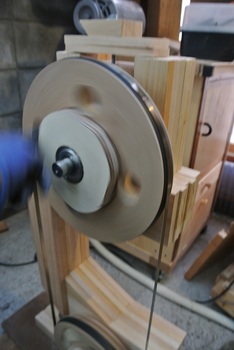
シャフトホルダーはそれに輪をかけて難関。
はっきり言って、バンドソーがあったほうがよい(笑)。
これが上ホイール用シャフトホルダの素材となる桜の端材ブロック。
プレーナーが掛かっているのは接する2面のみ。その直角も怪しい。
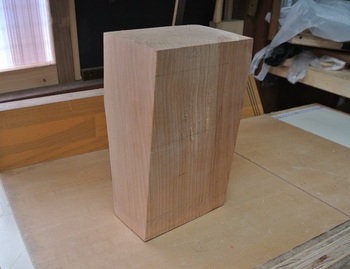
元はこの倍の幅があったのだが丸鋸で縦に挽き割って2分割にし、もう一方を下ホール用に。
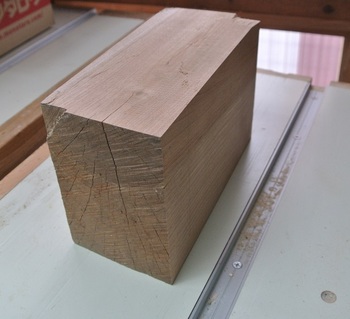
挽き割ると言っても、丸鋸なので裏表からせいぜい3cmづつ、少しづつ刃を入れる。裏表の平行が十分に出ていないため、切り口に段差ができる。せめて自動かんな等でちゃんとした面が出せればよかったのだが。
最大の鬼門はシャフトを通す20mmの長穴開け。
手持ちのフォスナービットと卓上ボール盤では、途中でテーブルをかさ上げしても60~70mmの深さがせいぜい。
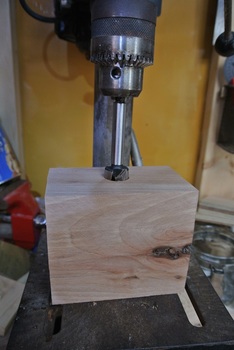
そこからは鉄工用のロングビットを使ってガイド穴を開け、
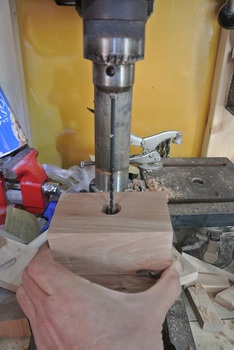
裏面からこのガイド穴を頼りに再度フォスナーで貫通穴を開けたが・・・・結果はこのとおり。
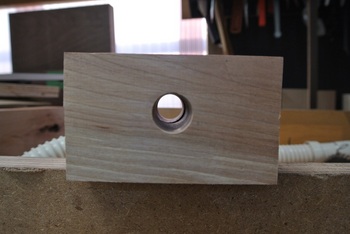
素直にロングビット
フォスナービットを突っ込んで段差を消したが、 シャフトを入れてみると途中から急にきつくなり、ハンマーで叩いてみるがほとんど動かない。時すでに遅し(^^;)。抜くに抜けず、ハンマーでたたくに叩いて、なんとかこの位置で押し込んだ・・・シャフトを抜くためにはブロック全体を破壊するしかない。
まあ、これで絶対に抜ける心配はない。
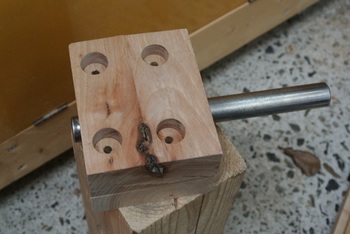
そのうえ、 対面の平行が出ていないのに無造作に両面から穴明けしたせいだろうが・・・・
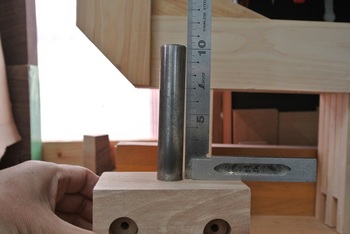
幸いしたのは、シャフト傾きは固定するフレーム前面に対して左右方向のため、ブロックを少し左に振って固定するだけでよい。
上下の傾きだとフレームとホルダーの間に薄板シムを入れて調整しなければならなくなる。
そして、これが上ホルダ。このシャフトも同じく抜けません(笑)
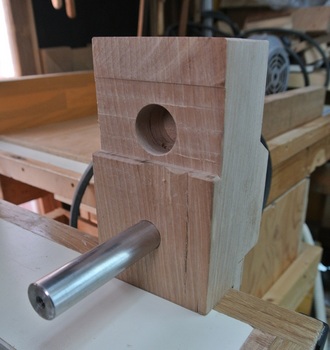
切り欠きが多く、それぼどの精度必要でないので、バンドソーがあれ楽勝なのだが、丸鋸テーブルとルーターで難儀したせいで思いっきり汚い仕上げ(^^;)
シャフトの上の穴には、ホルダーブロックの上から貫通穴を通したボルトを入れ、内部にこの叩いて曲げたワッシャ
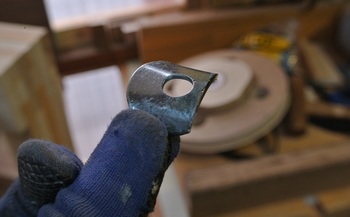
上ホルダ裏側には、上ホイールの前後の傾きを調節するM10ボルトを小さめの穴にねじ込む。この後、ボルトヘッド部分はグラインダーで切除。

下のホルダーは径6mm、長さ90mmの長ネジでフレーム下部に固定、上はフレーム頂きの二つの突起の間に載せ、ボルトで上に引っ張る。
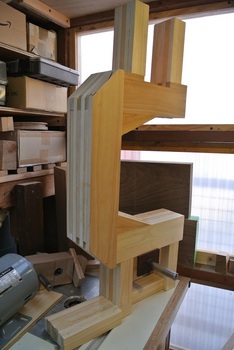
シャフトにホイールを通し、帯鋸刃を掛けてトラッキングの具合を確認する。
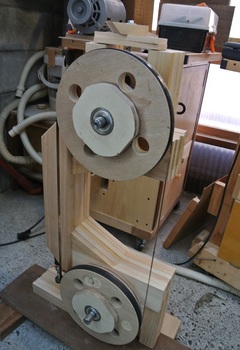
大体の場合うまくいくのだが、クラウンの角度がありすぎるせいか、時としてトラックの中心まで登り切れない場合がある。
クラウンの傾斜を緩くするよう切削したところ、しっかりとトラッキングするようになった。
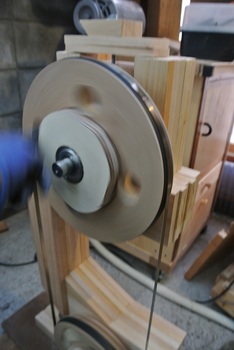
バンドソー(その3)ホイール製作の続き [バンドソー]
一応ホイールらしくなったが、
バンドソー用には、外周部の刃が当たる部分にクラウンを形作る必要がある。
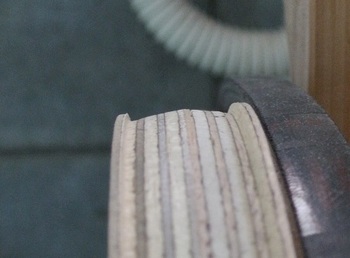
ここでいうクラウンが日本語で何と呼ばれるのか知らないが、「王冠」よりは、「山形形状の頂」という形そのものを指すのだろう。
回転するホイール上をトレースする帯鋸刃(フラットベルト)は、クラウンがあると自動的に高い部分に登る力が働くため、常にその中心をトラッキングする。一言で言えば自動調心機構か。
英文だが興味のある方はこちらを。
製作は旋盤のようにホイールを回して、ノミでクラウン形状に削る。
実際の作業は、ホイールを回すためのテンポラリー(一時)プーリーを作るところから。
合板をジグソーで粗切りした後、外周をストレートビットで切削。以前作った治具が役立つた。
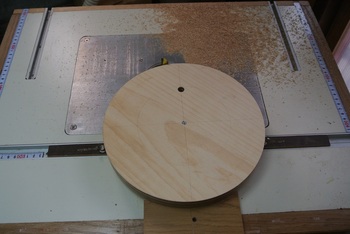
続いて、スロットカッター・ビット
で縦に溝を掘って、中心部をくり抜けば完成。溝が中心を外れているが、一時使用なので問題あるまい。

ちなみに溝幅は8mm(5/16インチ)
これをホイールにねじ止め。
シャフトとホイールもずれないよう固定し、さらにシャフトを作業用台座に挟み込み、動かないよう上からネジ止め。
モーター
を回したところ。インダクションモーターの静かさに感動!
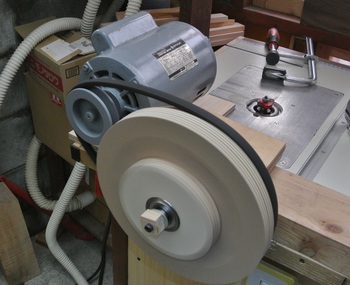
モーター
の回転数は約1700rpm、減速比1/3なのでホイールの回転数は570rpm、周速は秒速7.5m。これに刃を当てるわけだが・・・怖い、怖すぎる(笑)
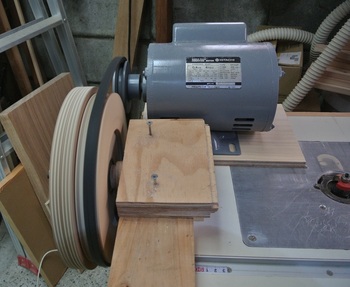
手に汗握りながら、恐る恐る刃を近づけるが、なかなか材に接触しない。
しばらくやっているうちに少しづつコツがつかめてきた。
・刃は上から下に回転する材の面に対し直角かむしろ若干俯角気味が安心感がある。
・鋭角に刃を当てると危険。刃が材に食い込んで、刃ごと回転方向に持っていかれる危険性がある。
・刃を置く支持材を切削箇所ぎりぎりまで近づけ、刃のぶれを極力少なくする。
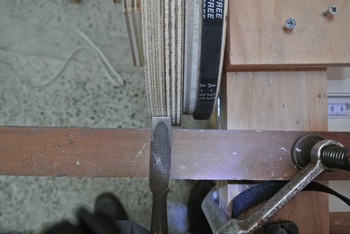
・切削初期、材料に凹凸が残っている間はショックが大きいので特に慎重に。その点、あらかじめ表面を平滑にしたことで大分楽になった。
・モーター、シャフトを固定するためのV字溝を付けた台座、切削用のノミを固定する支持材のすべてを堅牢な同一構造の上にしっかり固定する。
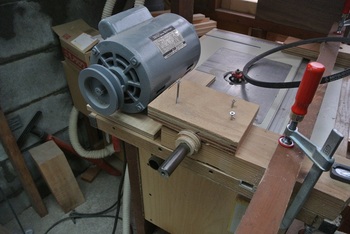
しかし、この後、フレームに全て組み付けた状態でクラウンの修正挽きをやったのだが、最初からこの方法ですればセッティングの二度手間が省けるかもしれない。
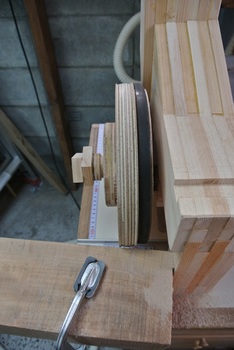
この一時旋盤作業、フェイスガード
に安全めがね
を着用したが、危険なことには変わりがない。また、写真のようなノミは本来の使い方ではないので、決して真似しないでください。
クラウン切削に入る前に、まず、真円に切削し外周長を確認する。
ルーターの削り残しの凹凸があるし、その後にベアリングを固定したため、偏芯している可能性がある。
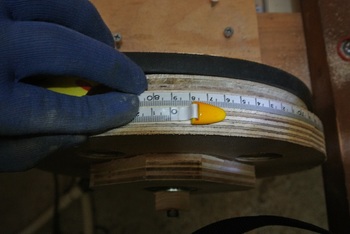
続いて、クラウンを形成する。
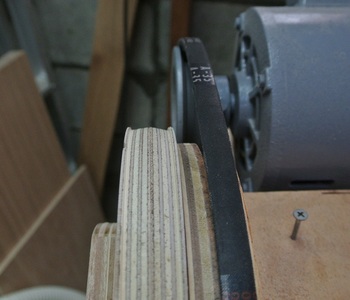
クラウンが機能する角度は4~5°とのことだが、この写真では明らかに削りすぎで、角度がつき過ぎている。
この後、修正切削。外周長が少し小さくなったが、この上に貼るゴムタイヤが厚めなためちょうど良かったかもしれない。
つづいて、駆動ホイールに付ける本プーリーの旋盤作業
すでに取り付けているテンポラリープーリーはそのままに、反対側に本プーリーを取り付けて、溝型を調節する。
本プーリーには、あらかじめルーターテーブルのスロットカッター・ビット
で幅6mmで溝を掘っておく。細いのみで溝の両側面にテーパーを付け、ベルト底が接しないよう溝の底をさらに彫り込む。
上から本プーリー(切削前)、ホイール、一時プーイー
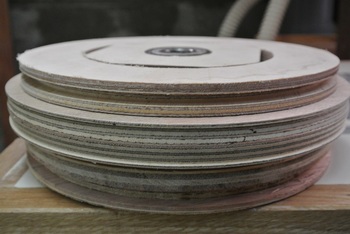
最後に、バランス調整。
直径25cmの円盤が高速回転するので、わずかなバランスの狂いで振動が出る。
シャフトを通す穴にさらに小径ベアリング
をはめ、細長いドライバを差し込んで重心の偏りを確認。重たい側のホイール側面を削って軽くする。
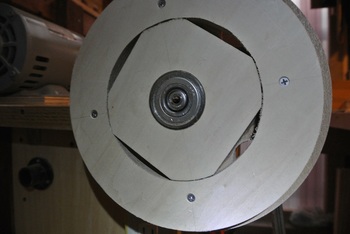
なんと、上ホイールは調整がいらなかった!下ホイールは後付けプーリーの芯が少しずれたせいか、3箇所に穴を掘る。
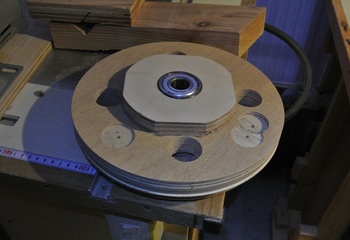
なお、トラック両側の削り残しは、ゴムタイヤ脱落防止のため。
オリジナルでは14インチホイールに対して12インチの自転車チューブ
でホイール外周全体をカバーしているが、10インチホイールにするとこれに合う自転車用チューブは見当たらない。
探した代替品
がこれ。
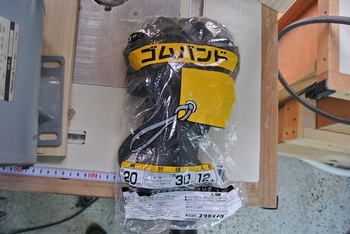
軽トラの荷台カバーなどに使用するバンドで、タイヤチューブの再生品のようだ。12本入りで安価だし、厚さも1mm以上あり自転車チューブよりは耐久性はありそう。折径30㎝とあるが、長さはまちまちで、
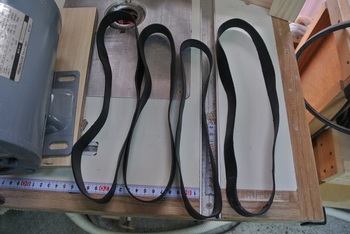
長さを変えてゴムテンションを選択できる。ただ、幅20mmでは引っ張ると幅が狭くなってトラック全面をカバーしきれないため、もう少し広めの方がよさそうだ
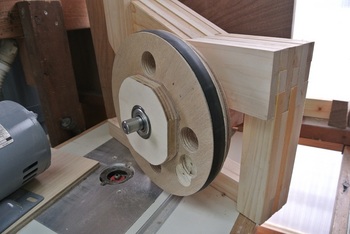
バンドソー用には、外周部の刃が当たる部分にクラウンを形作る必要がある。
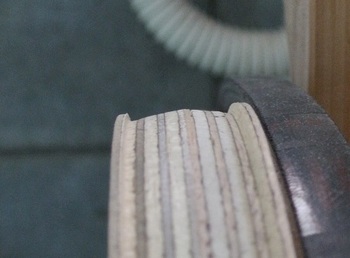
ここでいうクラウンが日本語で何と呼ばれるのか知らないが、「王冠」よりは、「山形形状の頂」という形そのものを指すのだろう。
回転するホイール上をトレースする帯鋸刃(フラットベルト)は、クラウンがあると自動的に高い部分に登る力が働くため、常にその中心をトラッキングする。一言で言えば自動調心機構か。
英文だが興味のある方はこちらを。
製作は旋盤のようにホイールを回して、ノミでクラウン形状に削る。
実際の作業は、ホイールを回すためのテンポラリー(一時)プーリーを作るところから。
合板をジグソーで粗切りした後、外周をストレートビットで切削。以前作った治具が役立つた。
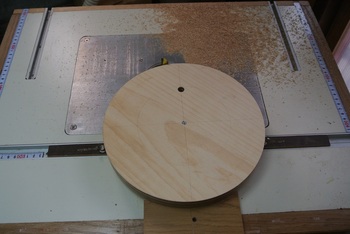
続いて、スロットカッター・ビット

ちなみに溝幅は8mm(5/16インチ)
これをホイールにねじ止め。
シャフトとホイールもずれないよう固定し、さらにシャフトを作業用台座に挟み込み、動かないよう上からネジ止め。
モーター
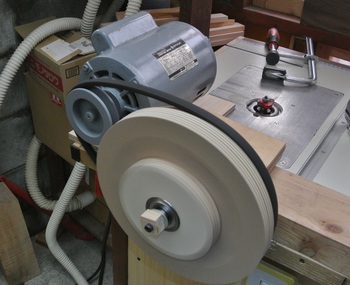
モーター
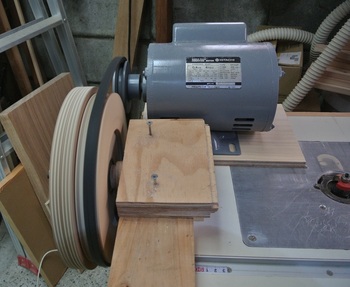
手に汗握りながら、恐る恐る刃を近づけるが、なかなか材に接触しない。
しばらくやっているうちに少しづつコツがつかめてきた。
・刃は上から下に回転する材の面に対し直角かむしろ若干俯角気味が安心感がある。
・鋭角に刃を当てると危険。刃が材に食い込んで、刃ごと回転方向に持っていかれる危険性がある。
・刃を置く支持材を切削箇所ぎりぎりまで近づけ、刃のぶれを極力少なくする。
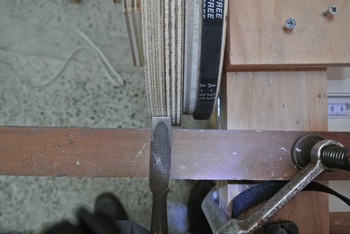
・切削初期、材料に凹凸が残っている間はショックが大きいので特に慎重に。その点、あらかじめ表面を平滑にしたことで大分楽になった。
・モーター、シャフトを固定するためのV字溝を付けた台座、切削用のノミを固定する支持材のすべてを堅牢な同一構造の上にしっかり固定する。
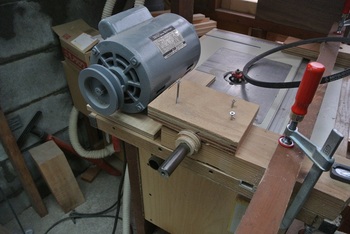
しかし、この後、フレームに全て組み付けた状態でクラウンの修正挽きをやったのだが、最初からこの方法ですればセッティングの二度手間が省けるかもしれない。
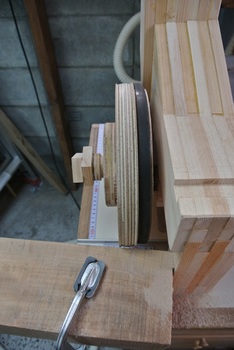
この一時旋盤作業、フェイスガード
クラウン切削に入る前に、まず、真円に切削し外周長を確認する。
ルーターの削り残しの凹凸があるし、その後にベアリングを固定したため、偏芯している可能性がある。
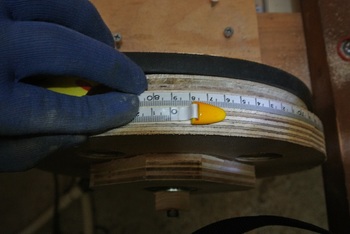
続いて、クラウンを形成する。
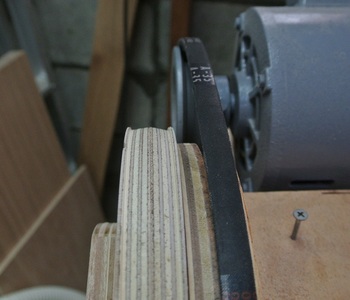
クラウンが機能する角度は4~5°とのことだが、この写真では明らかに削りすぎで、角度がつき過ぎている。
この後、修正切削。外周長が少し小さくなったが、この上に貼るゴムタイヤが厚めなためちょうど良かったかもしれない。
つづいて、駆動ホイールに付ける本プーリーの旋盤作業
すでに取り付けているテンポラリープーリーはそのままに、反対側に本プーリーを取り付けて、溝型を調節する。
本プーリーには、あらかじめルーターテーブルのスロットカッター・ビット
上から本プーリー(切削前)、ホイール、一時プーイー
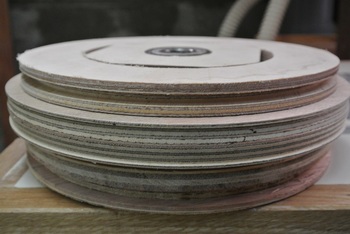
最後に、バランス調整。
直径25cmの円盤が高速回転するので、わずかなバランスの狂いで振動が出る。
シャフトを通す穴にさらに小径ベアリング
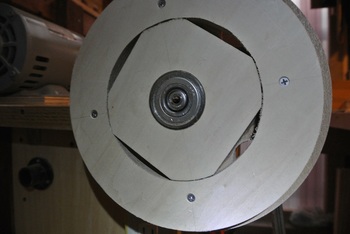
なんと、上ホイールは調整がいらなかった!下ホイールは後付けプーリーの芯が少しずれたせいか、3箇所に穴を掘る。
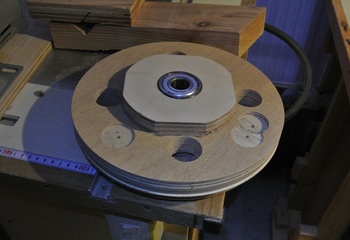
なお、トラック両側の削り残しは、ゴムタイヤ脱落防止のため。
オリジナルでは14インチホイールに対して12インチの自転車チューブ
探した代替品
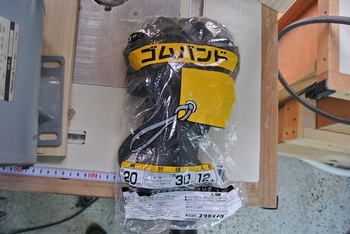
軽トラの荷台カバーなどに使用するバンドで、タイヤチューブの再生品のようだ。12本入りで安価だし、厚さも1mm以上あり自転車チューブよりは耐久性はありそう。折径30㎝とあるが、長さはまちまちで、
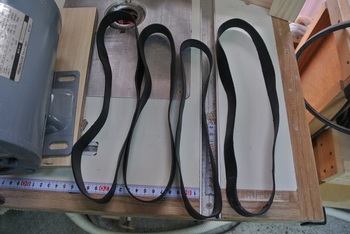
長さを変えてゴムテンションを選択できる。ただ、幅20mmでは引っ張ると幅が狭くなってトラック全面をカバーしきれないため、もう少し広めの方がよさそうだ
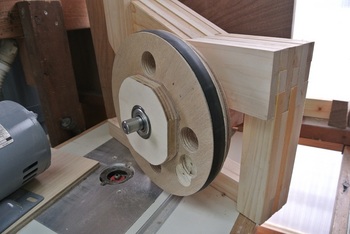
バンドソー(その2)ホイール製作 [バンドソー]
ここで、基本スペック
ホイール径 10インチ(25cm)
ホイールシャフト径 20mm(20cmのシャフトの手持ちが何故か1本あった・・・?)
バンド長 1840mm(レクソンの10インチやリョービの帯鋸刃
などが使える)
ホイール径とバンド長が決まれば、フレームサイズや挽き割り高などが自ずと決まってくる。
テーブル面の可動機構をどうするかにもよるが、CAD上での挽き割り高は21cm程度。
10インチバンドソーとしては、ほぼ限界に近いところか。
これが、ホイールを両側からサンドイッチする木製ベアリングユニット

ボールベアリング
を合板にたたき込んだもの。
フランジ付きのベアリングユニット
もあるが、木製ホイールへのボルト固定はホイールに局部的に大きな力がかかり木質劣化でよろしくないとのこと。むしろ、ボンドで面固定する方が安定した機能を維持できるというのは何となく理解できる。
なお、フランジの材質は強度に方向性がない合板指定。
ベアリングをはめる前の穴。ベアリング
の外形52mmより0.5mm程度は小さいか?貫通穴とせず、裏側から小さめの穴を空け段差を付けてストッパとする。

これにボールベアリング
を叩きこんで、最後は万力で締めて押し込む。

フランジ面に対してベアリングの平行を出すためのアライメント。

ダイヤルゲージ
を固定するスタンドは持っていないため、ボール盤のテーブルに磁石でゲージを固定してます(^^;)台座にはめた20mm径の丸棒にベアリングを差し込んで、フランジごとゆっくり回転させる。高くなっている部分は万力で締め、また測っての繰り返しで何とか0.05mm程度の凹凸に収める。
続いて、ホイール。
12mm合板の2枚合わせ。

外周を粗切りした後、ルーターテーブルでホイールを回転させながら外周切削。

ホイール中心に穴を空け、自作の芯出し治具(丸棒をベアリング
に差し込んだだけ)のベアリング
部を差し込んで、さらに丸棒部をホイールの下に隠れている台座の穴に差し込む。隠れて見えないが台座は上のベアリングアライメントのものと同じ。

続いて、ホイールの芯出し治具はそのまま残した状態で、丸棒部をベアリングユニットに差し込んで合体。双方の芯が出た状態で、接着。
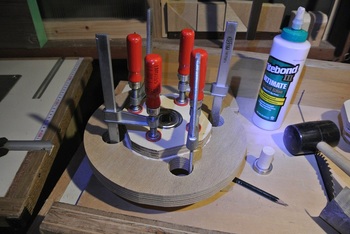
これが乾燥したら、治具を取り、実際のシャフトを差し込んでもう片方のベアリングユニットを固定する。
軸の傾きをこれでチェック。

シャフトが短いせいもあるがシャフトを固定する台座でもないと、ヴァンデル氏のようにハンマーで叩いて軸調整というのはなかなか難しい。仮にうまく合ったとしても、クランプを締めるとボンドを塗った面が滑ってしまう。微妙なさじ加減が必要なようだ。ホイールを回すと微妙に偏芯しているのがわかるが、少なくともシャフトの抜き差しさえできれば良しとすべきか。
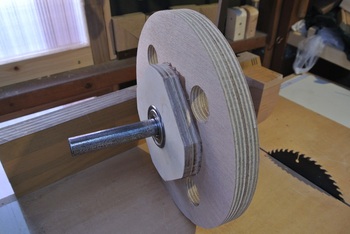
ホイール径 10インチ(25cm)
ホイールシャフト径 20mm(20cmのシャフトの手持ちが何故か1本あった・・・?)
バンド長 1840mm(レクソンの10インチやリョービの帯鋸刃
ホイール径とバンド長が決まれば、フレームサイズや挽き割り高などが自ずと決まってくる。
テーブル面の可動機構をどうするかにもよるが、CAD上での挽き割り高は21cm程度。
10インチバンドソーとしては、ほぼ限界に近いところか。
これが、ホイールを両側からサンドイッチする木製ベアリングユニット

ボールベアリング
フランジ付きのベアリングユニット
なお、フランジの材質は強度に方向性がない合板指定。
ベアリングをはめる前の穴。ベアリング

これにボールベアリング

フランジ面に対してベアリングの平行を出すためのアライメント。

ダイヤルゲージ
続いて、ホイール。
12mm合板の2枚合わせ。

外周を粗切りした後、ルーターテーブルでホイールを回転させながら外周切削。

ホイール中心に穴を空け、自作の芯出し治具(丸棒をベアリング

続いて、ホイールの芯出し治具はそのまま残した状態で、丸棒部をベアリングユニットに差し込んで合体。双方の芯が出た状態で、接着。
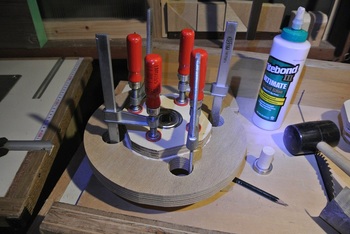
これが乾燥したら、治具を取り、実際のシャフトを差し込んでもう片方のベアリングユニットを固定する。
軸の傾きをこれでチェック。

シャフトが短いせいもあるがシャフトを固定する台座でもないと、ヴァンデル氏のようにハンマーで叩いて軸調整というのはなかなか難しい。仮にうまく合ったとしても、クランプを締めるとボンドを塗った面が滑ってしまう。微妙なさじ加減が必要なようだ。ホイールを回すと微妙に偏芯しているのがわかるが、少なくともシャフトの抜き差しさえできれば良しとすべきか。
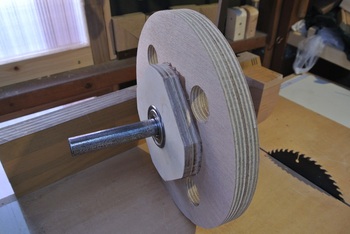
バンドソー(その1)フレーム製作 [バンドソー]
遅ればせながら、謹賀新年
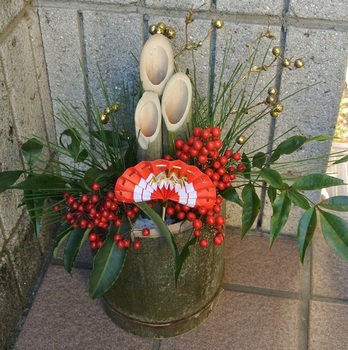
フレーム製作は1月以上前に始めたが、ついに新年を迎えてしまった。
かといって作業の難易度が高くわけではなくて、筆が遅いだけです。
フレーム製作の最大のポイントは、第1層目の垂直ポール部と上下の横メンバー部の直角及び並行を精度よく出すこと。加えて上下のメンバーに捻じれがないようにしっかりと平面を出すことのようです。
これが捻じれていると、積層工程では修正のしようがない。
正面側(ホイールがつく側)

裏側(積層していく側)
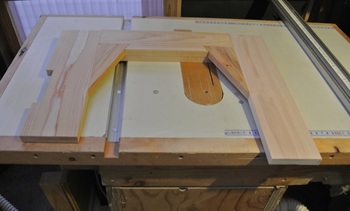
第一層目が正確に組めれば、これを基準面して、
丸鋸テーブルで切り出した材をボンド
で積み重ねていくだけ。
どんどん重ねたいところだが、う~ん、クランプが足りない!遅々として進まず。

板材接合面の段差は、こまめにカンナで削って平滑に。

オリジナルに倣って、ねじや釘は使わずボンド
のみで接合したせいで、
クランプで締めると、滑ってずれが生じてしまう。
適当に木ねじなどで位置決めをしたほうが作業効率の点でも良かったかもしれない。
ただ、奥行き方向の積層のずれはあまり神経質にならなくてよいようだ。
多少のずれがあっても、次の層で修正すればよいし、段差が邪魔になる部分は削って平滑にするというのがいかにも欧米流です。
強度を出すうえで重要な三角版。
角度出しのため基準を端材で作って材を切り出す。

サイズ合わせはオリジナルのビデオにある通り、やってみると以外に簡単。
オリジナルプランでは、板材の厚さを18mmまたは19mmとしているが、
10インチホイールにスケースダウンする観点から15mmとした。
これは、たまたま目に留まった良質のヒノキ材が15mm厚だったせいもある。
ここで問題なのは、サイズの縮小率。
オリジナル14インチをベースにするとスケールダウンは10/14だが、
問題は、単純に一律には小さくできないこと。
自重の支持や力点までの支持長などは単純に比例でよいと思われるが、例えば、上下のメンバーにかかるベルトテンションによる引っ張りはホイールサイズに拘わらず、同じような力が掛かると考えられる。・・・・とか、もっともらしいことを言ってるが、所詮文系人間、力学的な知識は中学生レベルしかありません(笑)。
くれぐれも真似しないようにしてください(笑)
ただ、横メンバーの幅などは、ホイール径が小さくなる以上、それに合わせて小さくしないと、他のサイズに影響が出るため、部位によって概ね0.7~0.9程度の縮小率とした。また、このプラン、フレームの奥行き方向の冗長性があるというか制約が少ないので、単純に積層数を増やして強度上げることができる。ここに至って、最初から厚めの板材を使った方がよかったと気づく(笑)。
そして、5層目まで組んだところ。

この後、オリジナルよりも一層多く積層することに。
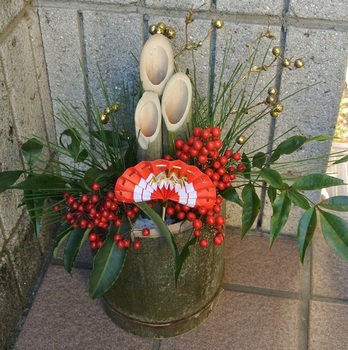
フレーム製作は1月以上前に始めたが、ついに新年を迎えてしまった。
かといって作業の難易度が高くわけではなくて、筆が遅いだけです。
フレーム製作の最大のポイントは、第1層目の垂直ポール部と上下の横メンバー部の直角及び並行を精度よく出すこと。加えて上下のメンバーに捻じれがないようにしっかりと平面を出すことのようです。
これが捻じれていると、積層工程では修正のしようがない。
正面側(ホイールがつく側)

裏側(積層していく側)
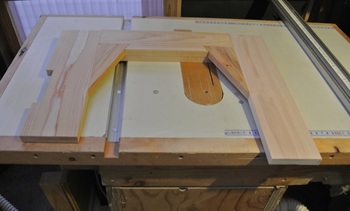
第一層目が正確に組めれば、これを基準面して、
丸鋸テーブルで切り出した材をボンド
どんどん重ねたいところだが、う~ん、クランプが足りない!遅々として進まず。

板材接合面の段差は、こまめにカンナで削って平滑に。

オリジナルに倣って、ねじや釘は使わずボンド
クランプで締めると、滑ってずれが生じてしまう。
適当に木ねじなどで位置決めをしたほうが作業効率の点でも良かったかもしれない。
ただ、奥行き方向の積層のずれはあまり神経質にならなくてよいようだ。
多少のずれがあっても、次の層で修正すればよいし、段差が邪魔になる部分は削って平滑にするというのがいかにも欧米流です。
強度を出すうえで重要な三角版。
角度出しのため基準を端材で作って材を切り出す。

サイズ合わせはオリジナルのビデオにある通り、やってみると以外に簡単。
オリジナルプランでは、板材の厚さを18mmまたは19mmとしているが、
10インチホイールにスケースダウンする観点から15mmとした。
これは、たまたま目に留まった良質のヒノキ材が15mm厚だったせいもある。
ここで問題なのは、サイズの縮小率。
オリジナル14インチをベースにするとスケールダウンは10/14だが、
問題は、単純に一律には小さくできないこと。
自重の支持や力点までの支持長などは単純に比例でよいと思われるが、例えば、上下のメンバーにかかるベルトテンションによる引っ張りはホイールサイズに拘わらず、同じような力が掛かると考えられる。・・・・とか、もっともらしいことを言ってるが、所詮文系人間、力学的な知識は中学生レベルしかありません(笑)。
くれぐれも真似しないようにしてください(笑)
ただ、横メンバーの幅などは、ホイール径が小さくなる以上、それに合わせて小さくしないと、他のサイズに影響が出るため、部位によって概ね0.7~0.9程度の縮小率とした。また、このプラン、フレームの奥行き方向の冗長性があるというか制約が少ないので、単純に積層数を増やして強度上げることができる。ここに至って、最初から厚めの板材を使った方がよかったと気づく(笑)。
そして、5層目まで組んだところ。
この後、オリジナルよりも一層多く積層することに。
バンドソーのこと [バンドソー]
う~ん、バンドソーが欲しい。
しかし、小さいのは中途半端な感じだし、本格的なものになるとかなり高価だし、大き過ぎて今の作業場には入りそうにない。
そんなことで、ずっと踏み出しかねていたところ、目に留まったのがこれ。
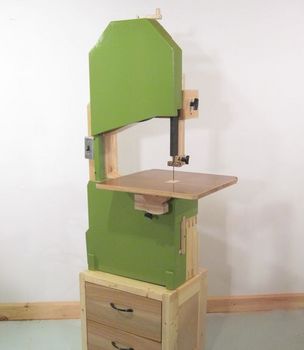
いつものMatthias Wandel氏のHPにあるやつ。
何とこれ、木製です。
要所にはハードウッドが使われているが、フレーム構造はSPFなどのソフトウッドのみ。ただ、木の強度特性を生かすべく、木目方向の選択や積層の木組みを最適化することで、構造的な強度は市販の鋳物フレームを上回るとある。
騒音や振動もかなり抑えられているみたい。
しかし、堅木ブロックの形成や大物の旋盤作業など今までやったとことのない作業もある。
要求される木工テクニックはかなり難易度の高そうだし、よく見ると、バンドソーや自動かんななどの機材がないと難しい感じもする。
いろいろ迷ったが、
まあ、必ずしも趣味が木工というのでははなくて、
メカへの興味というか、何でも自分で作ることが趣味というか・・・
工作がしたいのだろうな・・・と自分を納得させて自作することに(笑)
結局、ホイール径16インチと
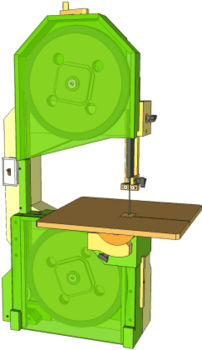
14インチ

の2つのプランを購入。為替手数料などを含めて3千円強を出費。
ただ、そのままのサイズだと自分の工房には大き過ぎるので、
基本的な構造やメカニズムなどはそのままに、10インチにスケールダウンすべく、元プランを基に、CADで図面を引いてみる。
重さは30㎏未満、高さ1m未満・・・なんとなかりそうな感じ。
さて、どうなることか。(つづく)